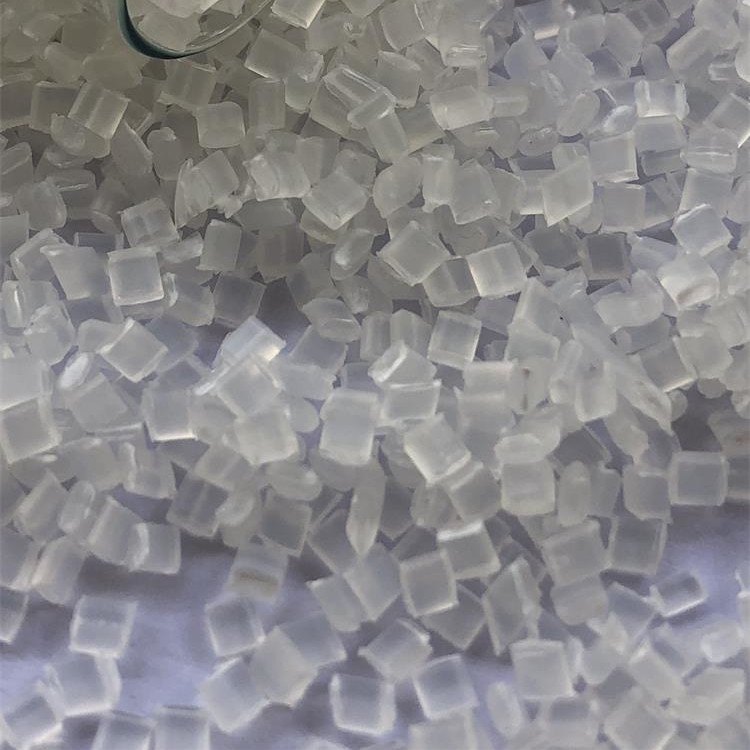
Enhancing Plastic Properties through Additive Masterbatch
The realm of plastic manufacturing stands as a vibrant and forward-thinking domain where perpetual advancement remains pivotal.
Electret masterbatch is a specially formulated additive used in the production of meltblown cloth, particularly in materials like those used for N95 masks. This additive plays a crucial role in enhancing the filtration efficiency of meltblown fabrics by enabling them to capture fine particles such as dust, aerosols, bacteria, and viruses.
According to the national YY0469-2004 “Technical Requirements for Medical Surgical Masks” standard, key technical indicators for medical surgical masks include filtration efficiency, bacterial filtration efficiency, and respiratory resistance. Professionals in the meltblown fabric industry understand that incorporating electret masterbatch into the meltblown material is essential for achieving effective filtration of fine particles.
Meltblown cloth without electret masterbatch primarily provides a mechanical barrier, resulting in a filtration efficiency of generally less than 50%. By adding electret masterbatch, the meltblown cloth becomes electrically charged, significantly improving its ability to adsorb particles as small as 0.3 microns. The electret masterbatch stores electric charges, creating an electrostatic field that attracts and captures particles, thereby increasing the filtration efficiency to levels of 90%, 95%, or even 99%.
The electret masterbatch works by enhancing the density and depth of charge trapping sites within the meltblown fabric. It effectively releases negative ions and stores charges, improving the overall filtration efficiency and resistance to thermal attenuation. This means that, under the same fiber fineness and weight, the electret-enhanced meltblown fabric can achieve higher filtration efficiency with lower resistance.
One common issue with meltblown cloth is the attenuation of its electrostatic charge over time. Initially, electret-enhanced meltblown fabric can achieve a filtration efficiency of 95+%, but this efficiency can decrease due to the instability of the electrostatic field and charge attenuation. To combat this, it is crucial to use electret masterbatches that offer long-term charge retention and excellent compatibility with meltblown materials.
To produce high-efficiency and high-quality meltblown cloth, it is important to select a high-performance electret masterbatch and ensure it is compatible with the meltblown material. Additionally, factors such as the meltblown process, screw design, spinneret configuration, and voltage settings play significant roles in the overall performance of the meltblown fabric.
By integrating a superior electret masterbatch with meltblown polypropylene (PP) material, manufacturers can effectively address the challenges of charge attenuation and achieve consistent high filtration efficiency, ensuring the production of top-quality meltblown fabrics suitable for critical applications like medical masks and air filters.
Incorporating electret masterbatch into the production of meltblown cloth is essential for achieving high filtration efficiency, vital for applications like medical masks and air filters. This additive enhances the fabric’s ability to capture fine particles by creating an electrostatic charge, significantly improving its performance. By choosing high-quality electret masterbatch and ensuring compatibility with the meltblown process, manufacturers can produce superior meltblown fabrics that meet stringent technical standards and maintain long-term efficiency.
Learn more knowledge and trends in masterbatch industry from our blog.
The realm of plastic manufacturing stands as a vibrant and forward-thinking domain where perpetual advancement remains pivotal.
White masterbatch is a highly versatile and essential component in various manufacturing processes, designed to impart brilliant whiteness, opacity, and uniform dispersion to finished products.
Masterbatch has become a cornerstone in the plastic manufacturing industry, widely used across diverse applications to enhance the properties and appearance of plastic products. From the automotive sector to packaging, masterbatch plays an essential role.
©2023. Masterbatch Manufacturer All Rights Reserved.
Our team will send back the best offer in 20 minutes.