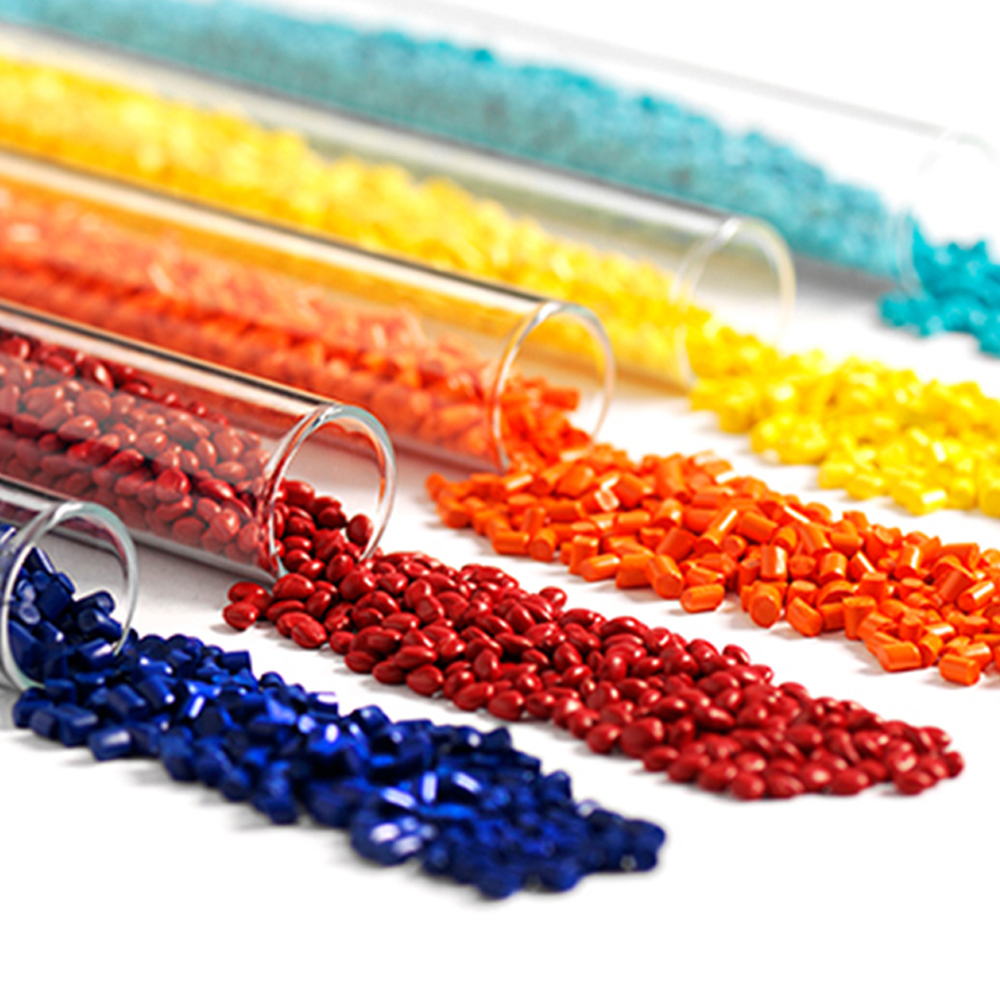
Exploring Diverse Filler Masterbatch Options for Enhanced Packaging Solutions
The plastic industry has witnessed remarkable growth in recent decades, propelled by rapid modernization and technological advancements
In this article, we delve into the realm of UV Masterbatch, exploring its composition, functionality, and why it is an indispensable addition to the plastic manufacturing process.
UV Masterbatch plays a pivotal role in shielding plastic products against the adverse effects of UV radiation. Its primary function is to prevent the absorption of damaging UV rays, thus fortifying the mechanical attributes and elongating the lifespan of plastic products.
Our UV Masterbatch finds applications in an array of industries, predominantly for UV resistance. Incorporating UV Masterbatch into the plastic production process yields benefits such as enhanced thermal stability, augmented durability, and, most importantly, UV protection.
The integration of UV Masterbatch into various plastic products yields a host of advantages, with some key benefits being:
UV Resistance: Plastic products fortified with UV Masterbatch exhibit remarkable resistance to the deteriorating effects of sunlight exposure.
Low Volatility and Extraction Resistance: UV Masterbatch ensures minimal interaction with surrounding elements, translating into lower volatility and extraction resistance.
Extended Service Life and Reduced Costs: Enhanced UV protection contributes to a prolonged product lifespan, thereby reducing overall replacement costs.
Superior Surface Quality: Products infused with UV Masterbatch exhibit superior surface characteristics, adding to their aesthetic appeal.
Minimal Interaction with Pigments and Fillers: The presence of UV Masterbatch minimizes undesirable interactions with pigments and fillers, ensuring consistent product quality.
Long-Term UV Resistance and Product Durability: The incorporation of UV Masterbatch results in long-lasting UV resistance, guaranteeing the product’s durability.
UV Masterbatch is available in concentrations ranging from 10% to 20%, incorporating high-quality Hindered Amine Light Stabilizers (HALS). This ensures optimum UV stability to meet the rigorous demands of various industries and plastic products.
UV radiation, often referred to as Ultraviolet radiation, spans the electromagnetic spectrum between X-rays and visible light. While sunlight is the primary natural source of UV radiation, several artificial sources, such as fluorescent lights, curing lamps, and tanning booths, also emit harmful UV rays.
UV radiation poses a significant threat to both human health and the integrity of plastic products. It can lead to detrimental alterations in the composition, structure, and appearance of plastics. These alterations include cracking, chalking, color shifts, and loss of physical properties. Exposure to UV radiation can be particularly detrimental to the durability of plastic products, as it initiates a process known as photodegradation.
Photodegradation results from the breakdown of chemical bonds in polymers due to UV radiation, leading to the degradation of plastic products. To counteract this degradation, UV Masterbatch is employed in the manufacturing process, effectively mitigating the harmful effects of UV radiation.
High temperatures and exposure to UV radiation can wreak havoc on plastic products, leading to deformation, cracking, and loss of functionality. A clear example is the damage inflicted upon plastic sunglasses left in a hot car—high temperatures and UV radiation can cause the lenses and frames to deteriorate.
The inclusion of UV Masterbatch in the plastic production process is paramount to shield against the ravages of UV radiation. By doing so, plastic products become exceptionally resilient and durable, maintaining their form and function under various conditions.
UV Masterbatch serves as a safeguard, prolonging the life of plastic products. It shields the polymers from UV rays, preventing their degradation when exposed to direct sunlight or outdoor conditions. Incorporating UV Masterbatch not only enhances product longevity but also reduces manufacturing costs, thanks to the higher quality of the end products.
In conclusion, UV Masterbatch plays a pivotal role in safeguarding plastic products from the adverse effects of UV radiation. Its inclusion in the manufacturing process elevates product stability, durability, longevity, and overall quality. By embracing UV Masterbatch, such as Tosaf’s offering, in the production of plastic goods, manufacturers can ensure maximum UV radiation blocking efficiency and elevate the performance of their products.
Learn more knowledge and trends in masterbatch industry from our blog.
The plastic industry has witnessed remarkable growth in recent decades, propelled by rapid modernization and technological advancements
PET color masterbatch, which consists of colored plastic pellets, plays a significant role in a variety of products that we use daily. Understanding the properties and characteristics of PET plastic resins can help both manufacturers and consumers ensure safe and efficient product use.
In the ever-evolving world of plastics, white masterbatch plays a crucial role in optimizing the quality and performance of plastic products. This article delves into the significance of white masterbatch, its applications, and its impact on the plastic industry.
©2023. Masterbatch Manufacturer All Rights Reserved.
Our team will send back the best offer in 20 minutes.