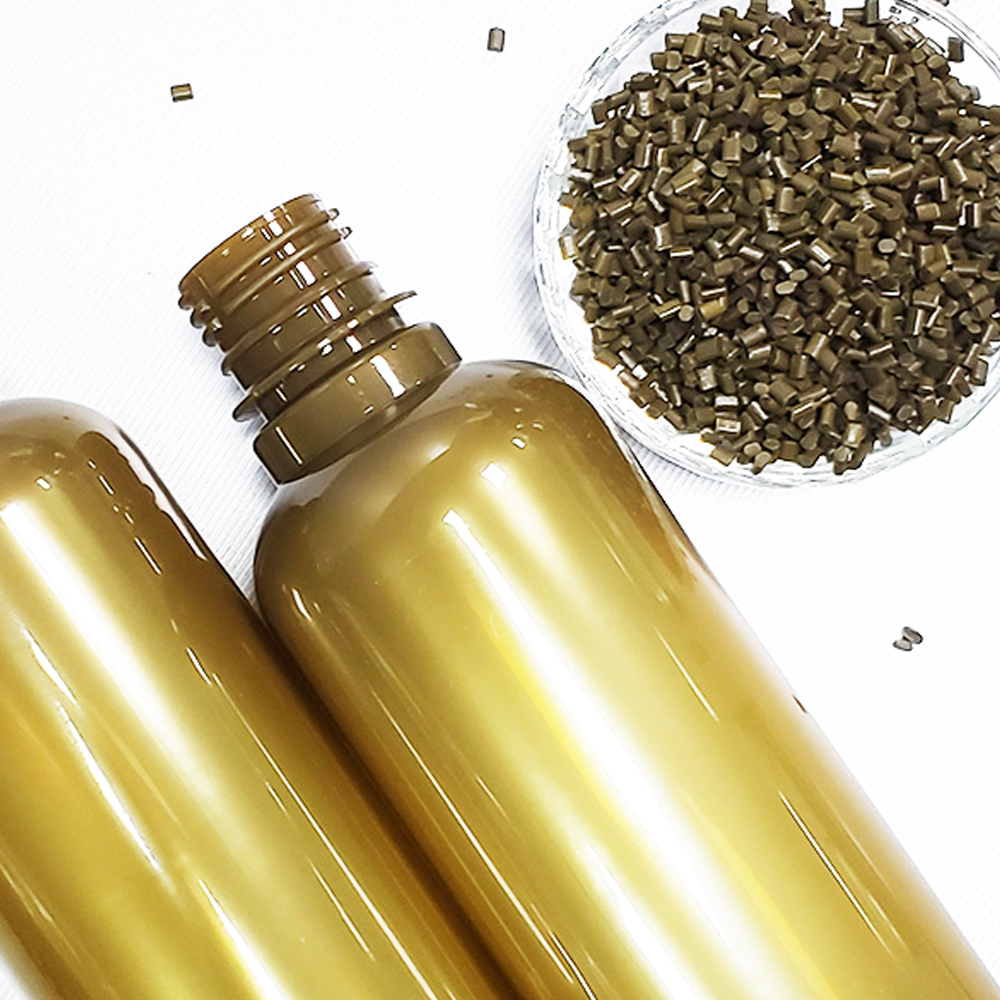
Unlocking Radiance: The Dynamic Role of Metallic Masterbatches in the Plastic Industry
Metallic masterbatches stand as versatile powerhouses within the realm of the plastic industry, wielding a transformative influence across various applications.
Understanding masterbatch is crucial for anyone involved in plastic manufacturing, as it can significantly impact product quality and production efficiency. Dive into this comprehensive guide to discover how masterbatch can elevate your plastic solutions.
Masterbatch is a concentrated mixture of pigments, additives, and polymers that are used to color or enhance the properties of plastic products. Typically available in pellet form, masterbatch is added to the base polymer during processing, such as extrusion or injection molding. This allows manufacturers to achieve consistent color and performance across their products.Masterbatches can be categorized into color masterbatches, which provide specific colors, and additive masterbatches, which enhance properties such as UV resistance, flame retardancy, or anti-static characteristics. The versatility of masterbatch makes it an essential component in the production of various plastic items, from packaging materials to automotive parts.
Masterbatch functions as an additive by allowing manufacturers to incorporate specific properties into their plastic products without altering the base polymer significantly. When added during processing, masterbatch disperses evenly throughout the polymer matrix, ensuring that the desired characteristics are uniformly distributed.For example, a color masterbatch can provide vibrant hues to plastic products, while an additive masterbatch can improve durability or resistance to environmental factors. This flexibility enables manufacturers to tailor their products to meet specific market demands and regulatory requirements.
There are several types of masterbatches, each designed for different applications and functionalities:
Understanding the different types of masterbatches is crucial for manufacturers looking to optimize their production processes and meet customer expectations.
Polymer compatibility is a critical factor in the effectiveness of masterbatch. When selecting a masterbatch, it is essential to ensure that it is compatible with the base polymer being used. Incompatible masterbatches can lead to poor dispersion, resulting in uneven color or performance issues in the final product.For instance, a masterbatch designed for polyethylene (PE) may not perform well when mixed with polypropylene (PP). Manufacturers should consult with masterbatch suppliers to ensure that the chosen product is suitable for their specific polymer and processing conditions.
Pigments are a fundamental component of color masterbatches, providing the desired color and opacity to plastic products. The choice of pigment can significantly affect the final product’s appearance, durability, and performance. Common pigments used in masterbatches include titanium dioxide (TiO2) for whiteness and opacity, as well as various organic and inorganic pigments for a wide range of colors.The quality of pigments also influences the overall performance of the masterbatch. High-quality pigments ensure better dispersion, stability, and resistance to fading over time, which is essential for products exposed to sunlight or harsh environments.
One of the key benefits of using masterbatch is its ability to enhance product consistency and process stability. By providing a uniform distribution of color and additives, masterbatch ensures that each batch of plastic products meets the same quality standards. This consistency is crucial for manufacturers who need to maintain brand integrity and customer satisfaction.Moreover, masterbatch can improve process stability during manufacturing. For example, using a well-formulated masterbatch can reduce the risk of defects such as streaking or color variations, leading to smoother production runs and less downtime.
The benefits of using masterbatch in plastic manufacturing are numerous:
These advantages make masterbatch an indispensable tool for manufacturers looking to optimize their plastic products.
Creating custom color masterbatch involves several steps, including formulation, testing, and production. Manufacturers typically start by identifying the desired color and performance characteristics. They then work with masterbatch suppliers to develop a formulation that meets these specifications.Once a formulation is established, it undergoes rigorous testing to ensure that it achieves the desired color and performance in the final product. After successful testing, the custom color masterbatch is produced in larger quantities for use in manufacturing.This process allows manufacturers to create unique products that stand out in the market, catering to specific customer preferences and industry trends.
The masterbatch industry is continually evolving, with new technologies and innovations emerging to enhance performance and sustainability. Some notable trends include:
These innovations are shaping the future of masterbatch technology, enabling manufacturers to create more efficient and sustainable plastic products.
Selecting the right masterbatch manufacturer is crucial for ensuring product quality and consistency. Here are some key factors to consider:
By carefully evaluating potential suppliers, manufacturers can find a partner that aligns with their needs and helps them achieve their production goals.
Masterbatch is an essential additive in the plastic industry, providing numerous benefits that enhance product quality and manufacturing efficiency. By understanding the various types of masterbatches, their applications, and the importance of polymer compatibility, manufacturers can make informed decisions that lead to superior plastic products.
By leveraging the advantages of masterbatch, manufacturers can create high-quality, competitive plastic products that meet the demands of today’s market.
Learn more knowledge and trends in masterbatch industry from our blog.
Metallic masterbatches stand as versatile powerhouses within the realm of the plastic industry, wielding a transformative influence across various applications.
Black masterbatch, a high-carbon black concentration additive ranging from 15% to 50%, takes center stage in this industry-focused blog. We’ll delve into its role in imparting black color to a diverse array of everyday items and uncover the benefits it offers.
In brief, masterbatch serves as a solid plastic additive utilized for coloring plastics or enhancing their properties.
©2023. Masterbatch Manufacturer All Rights Reserved.
Our team will send back the best offer in 20 minutes.