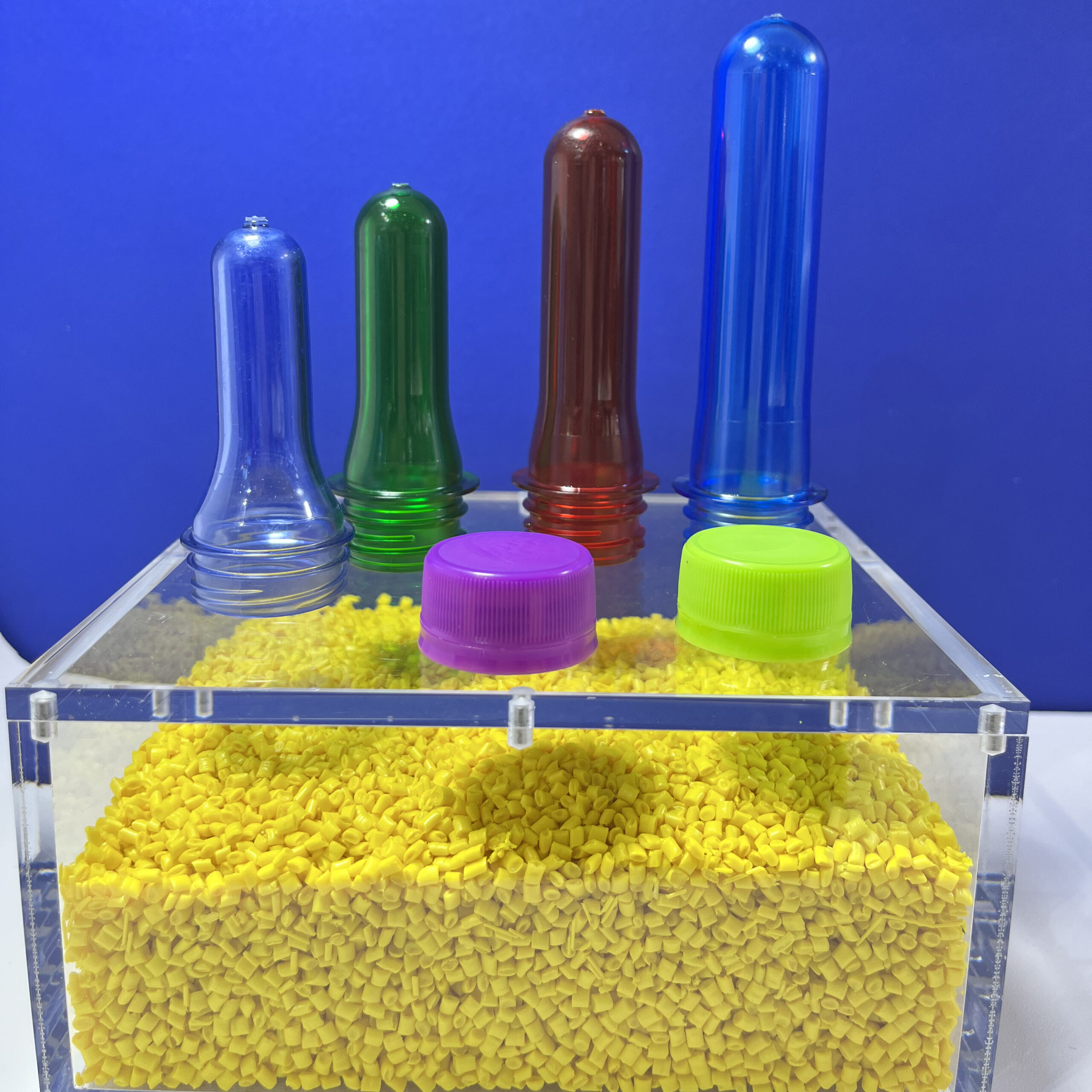
What is Masterbatch and Its Applications?
Masterbatch is a solid or liquid additive for plastic used for coloring plastics (color masterbatch) or imparting other properties to plastics (additive masterbatch).
As explained on Wikipedia, masterbatch is a concentrated blend of pigments or additives encapsulated into a carrier resin during a heating process. Once cooled, it is shaped into granules. This allows manufacturers to efficiently add color or properties to raw polymer materials during the production process.
Masterbatch requires less storage space compared to pre-compounded materials, enabling manufacturers to reduce stock holdings while maintaining flexibility in production.
Pigments and additives in masterbatch are pre-dispersed, ensuring even distribution throughout the polymer and enhancing the quality of the final product.
Unlike fine powder additives, masterbatch is dust-free, minimizing health risks and creating a cleaner work environment. This makes handling safer and reduces cleanup requirements.
Masterbatch suppliers take responsibility for color formulation and consistency, eliminating the need for trial-and-error adjustments. This ensures repeatable results across production batches.
Masterbatch reduces the time and expense associated with cleaning equipment and transitioning between production runs, making it cost-efficient.
Masterbatch offers a wide range of customizable colors and properties. Unlike fully compounded materials, it provides greater flexibility for creating variations in color and functional additives.
Factories using masterbatch can stock fewer grades of polymers and buy cost-effective natural polymers in bulk.
Masterbatch is often highly concentrated, enabling precise dosing for small amounts of expensive additives. For example, one 25 kg bag of masterbatch can process up to one ton of natural polymer.
Solid masterbatch is solvent-free, eliminating concerns about solvent evaporation. This ensures a longer shelf life compared to other additive forms.
The effectiveness of masterbatch depends on factors such as:
Masterbatch production involves two primary steps:
Key elements that impact masterbatch quality include the formulation, raw materials, and equipment used.
Iplastar provides a diverse range of masterbatches for various applications, tailored to meet customer requirements. These include:
Masterbatch is widely used across industries, including:
By leveraging the benefits of masterbatch, industries can achieve greater efficiency, versatility, and quality in plastic production.
Learn more knowledge and trends in masterbatch industry from our blog.
Masterbatch is a solid or liquid additive for plastic used for coloring plastics (color masterbatch) or imparting other properties to plastics (additive masterbatch).
The realm of plastic manufacturing stands as a vibrant and forward-thinking domain where perpetual advancement remains pivotal.
Black masterbatch is a crucial component in the plastics industry, serving as a concentrated mixture of carbon black and carrier resins that provides color and functional properties to plastic products.
©2023. Masterbatch Manufacturer All Rights Reserved.
Our team will send back the best offer in 20 minutes.