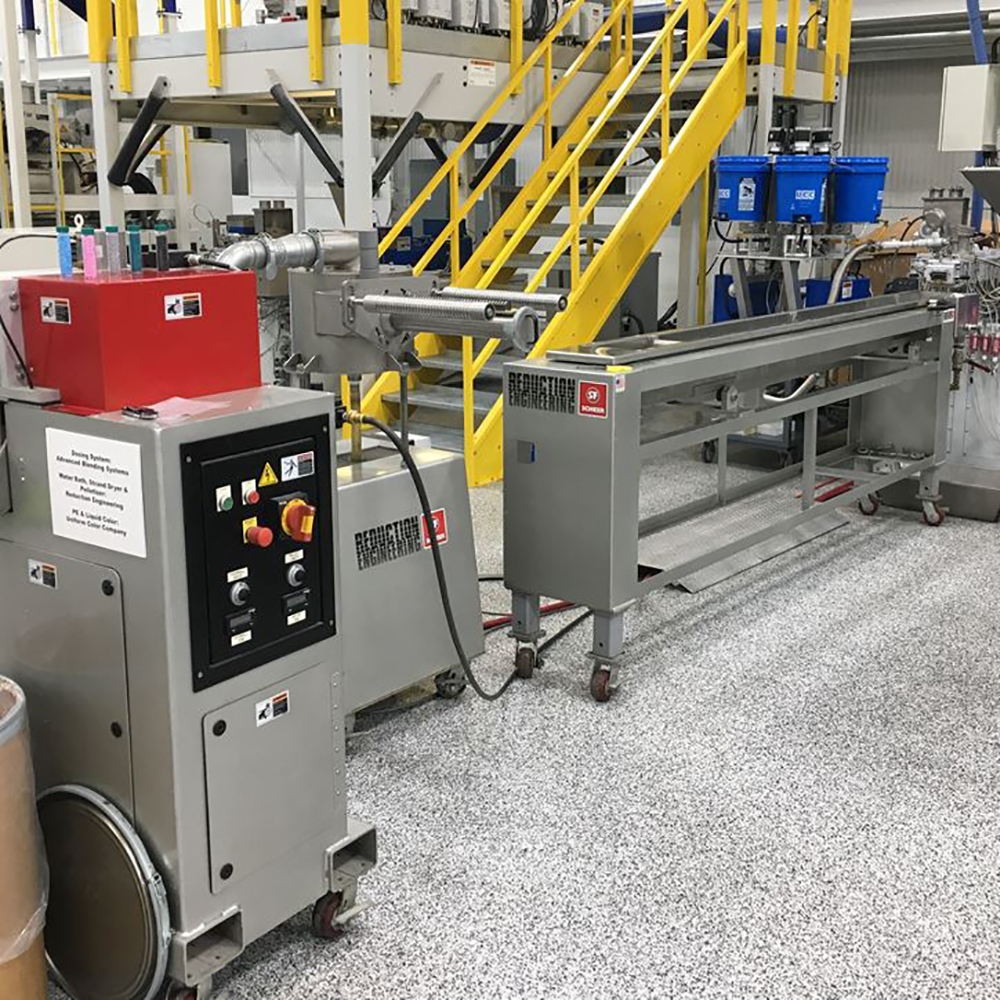
Advantages of Using Masterbatch in Plastic Production
Masterbatch (MB) is an additive used in plastic production to enhance properties or introduce color. It can be either solid or liquid and is categorized as either color masterbatch for coloring plastics or additive masterbatch for imparting other specific features.