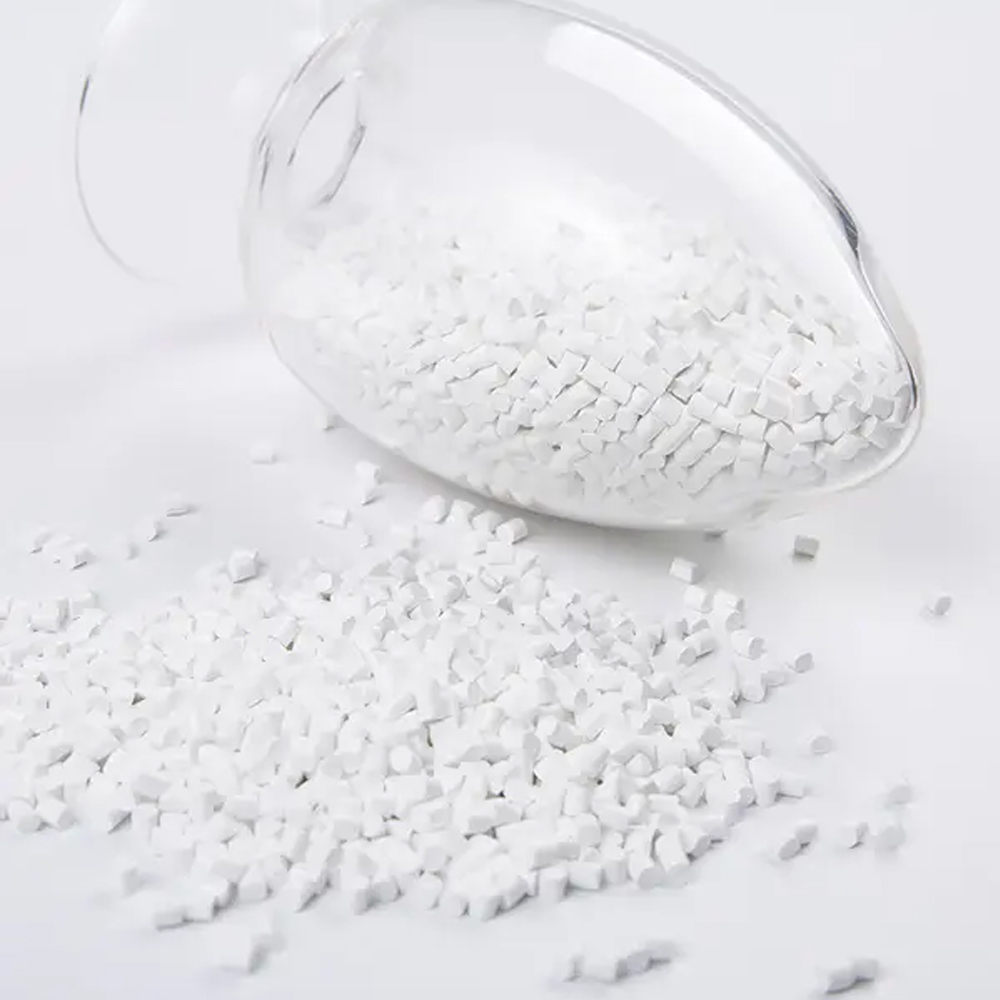
Applications of Masterbatch: Exploring a Range of Industries
For businesses operating in sectors such as packaging, automotive, consumer goods, construction, or textiles, familiarity with Masterbatch is likely crucial in the manufacturing process.
Key steps include selecting high-quality raw materials like carbon black pigments, carrier resins, and additives. These materials are mixed and compounded in a twin-screw extruder, where they undergo melting, mixing, and degassing to ensure uniform dispersion and remove volatile components. The molten material is then pelletized into uniform lengths and subjected to rigorous quality control testing. This process ensures the production of high-quality masterbatch, which is essential for creating black-colored plastic products with enhanced aesthetics, functionality, and performance, widely used in the plastics industry.
The production of melt-blown black masterbatch color masterbatch is a meticulous process that combines various components to achieve the desired color and dispersion qualities. This process typically involves using twin-screw extruders or similar compounding machinery to mix, disperse, and pelletize the masterbatch ingredients effectively. Here, we detail the key steps in the manufacturing process of melt-blown black masterbatch color masterbatch.
The initial step involves choosing high-quality raw materials, including pigments, carrier resins, and additives. Carbon black is a preferred pigment for its superior black color, UV resistance, and thermal stability. Carrier resins like polyethylene (PE) or polypropylene (PP) are selected based on their compatibility with the final product’s polymer matrix. Additives such as dispersing agents, processing aids, and stabilizers may also be included to enhance dispersion and processing characteristics.
After selecting the raw materials, they are accurately weighed and blended according to the desired formulation. The pigments, carrier resin, and additives are fed into the hopper of the twin-screw extruder in precise proportions. Inside the extruder, the materials undergo intense mechanical and thermal energy as they move along the screws.
As the materials advance through the extruder, they are exposed to increasing temperatures and pressure. The screws inside the extruder impart mechanical shear forces and distributive mixing action, ensuring thorough dispersion of the pigments within the carrier resin. The combination of heat and shear forces melts the resin, allowing the pigments to spread evenly throughout the polymer matrix.
During compounding, volatile components like moisture and air can become trapped within the melt. To eliminate these gases and ensure uniformity, the melt undergoes a degassing stage, typically using vacuum vents or degassing zones within the extruder barrel. Degassing helps prevent surface defects and ensures the final product’s quality.
Once the masterbatch formulation is homogenized and degassed, it is extruded through a die to form continuous strands of molten material. These strands are then quickly cooled and solidified using water or air, resulting in cylindrical pellets. The pellets are cut into uniform lengths using pelletizing equipment.
Throughout the manufacturing process, stringent quality control measures are implemented to ensure consistency and adherence to specifications. Samples of the masterbatch are tested for color intensity, dispersion, melt flow properties, thermal stability, and other performance parameters. Any deviations from the desired specifications are promptly addressed to maintain product quality.
The manufacturing of melt-blown black masterbatch color masterbatch is a complex and precise operation requiring expertise and rigorous quality control. By compounding pigments, carrier resins, and additives with twin-screw extruders, manufacturers achieve uniform dispersion and color consistency in the final product. This masterbatch is a crucial additive in the plastics industry, enabling the production of black-colored plastic products with improved aesthetics, functionality, and performance characteristics.
Learn more knowledge and trends in masterbatch industry from our blog.
For businesses operating in sectors such as packaging, automotive, consumer goods, construction, or textiles, familiarity with Masterbatch is likely crucial in the manufacturing process.
In the realm of plastic product manufacturing, safety stands as a paramount concern. Beyond its role in achieving consistent color and properties, masterbatch proves to be a crucial element in ensuring both your safety and the safety of the products you create.
Electret masterbatch is a specially formulated additive that significantly enhances the filtration efficiency of meltblown fabrics by enabling them to capture fine particles through an electrostatic charge.
©2023. Masterbatch Manufacturer All Rights Reserved.
Our team will send back the best offer in 20 minutes.