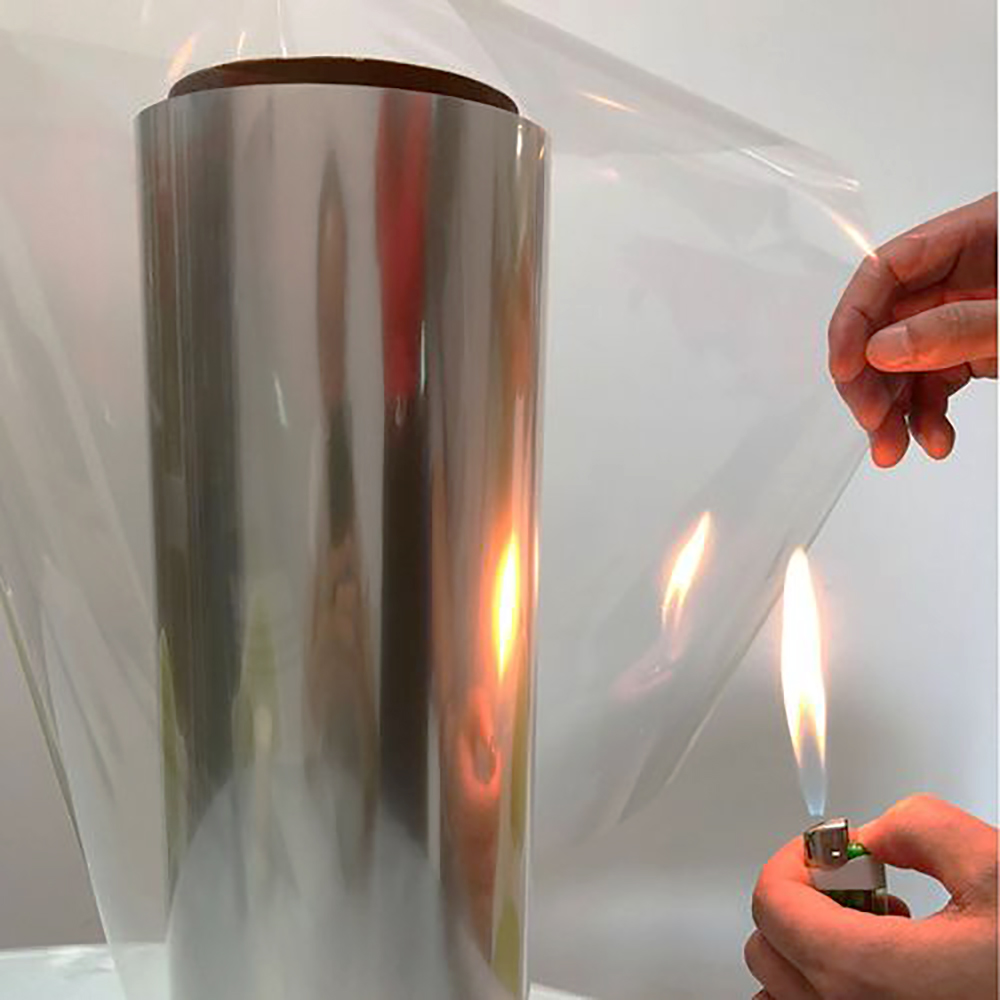
Flame Retardant Masterbatch: Enhancing Safety and Performance in Plastics
Flame Retardant Masterbatch is added to raw polymers during the manufacturing process of plastic products. This unique additive is added in order to provide the manufactured product with qualities that prevent potential flames from spreading.