Mastering Core: The Art of PET Black Masterbatch Production
Especially when the objective is to create ethereally soft and comfortable textiles with filmy spinning fibers. In this exploration, we delve into the realm of PET black masterbatch production, shedding light on the intricate process that yields outstanding results.
Table of Contents
Polyester fibers, versatile and omnipresent, find their applications in diverse industries. From automobile construction, where they form the foundation of roof linings, interior cladding, seat covers, and even convertible soft-tops, to the fashion sector, where they contribute to functional wear and street clothing, and the realm of home textiles, comprising curtains, seat covers, and more, polyester fibers play a pivotal role. The nuances in their application lie in factors such as fineness, cutting lengths, and various physical parameters, including fiber strength, elongation, and hot-air shrinkage.
The journey from raw materials to the creation of polyester fibers involves a meticulous process. Polyester fibers, made from PET (polyethylene terephthalate), undergo melt spinning. Here, the PET melt, compounded in an extruder, is carefully squeezed through spinnerets, culminating in the desired properties. To achieve specific characteristics, functional additives and pigments are introduced, typically in the form of masterbatches. These masterbatches are held to stringent requirements, particularly when crafting ultra-thin polyester fibers measuring just a few micrometers in thickness to produce exceptionally soft and comfortable textiles.
Meeting the elevated standards demanded by the industry, PET black masterbatches step into the spotlight when it comes to coloring polyester fibers. These masterbatches play a pivotal role in the compounding of PET, infusing black hues into the fibers. However, not all carbon black varieties make the cut; only those that are exceptionally pure and boast finely dispersed particles are deemed suitable. The secret lies in the utilization of industrially manufactured, cutting-edge carbon black—physically and chemically specified, and produced under tightly controlled processing conditions. Industrial carbon black comprises over 96% carbon, with minimal traces of oxygen, hydrogen, nitrogen, and sulfur. The availability of various types of carbon black further allows tailoring to specific applications.
Crafting color batches for fiber applications demands PET with a specific intrinsic viscosity (IV) falling within the range of 0.6 to 0.8 dl/g. The IV value serves as a comparative measure of the average molecular weight. However, this delicate process requires careful consideration, as water can significantly degrade molten PET hydrolytically. Simultaneously, PET’s hygroscopic nature means it can swiftly absorb water, reaching an equilibrium moisture content of up to 3,300 ppm.
In conclusion, the world of PET black masterbatch is one of precision, where every step in the process contributes to the creation of extraordinary polyester fibers. With a focus on excellence and adherence to stringent standards, PET black masterbatches stand as the cornerstone in the art of crafting soft, comfortable, and beautifully colored textiles.
Tags
More Blogs
Learn more knowledge and trends in masterbatch industry from our blog.

White Masterbatch: Unveiling Characteristics, Applications, and Benefits
Masterbatch, a potent blend of pigments and additives, serves as a vital ingredient in the plastic industry. White masterbatch, specifically, is a plastic enhancer tasked with bestowing a brilliant, white hue to plastic products.
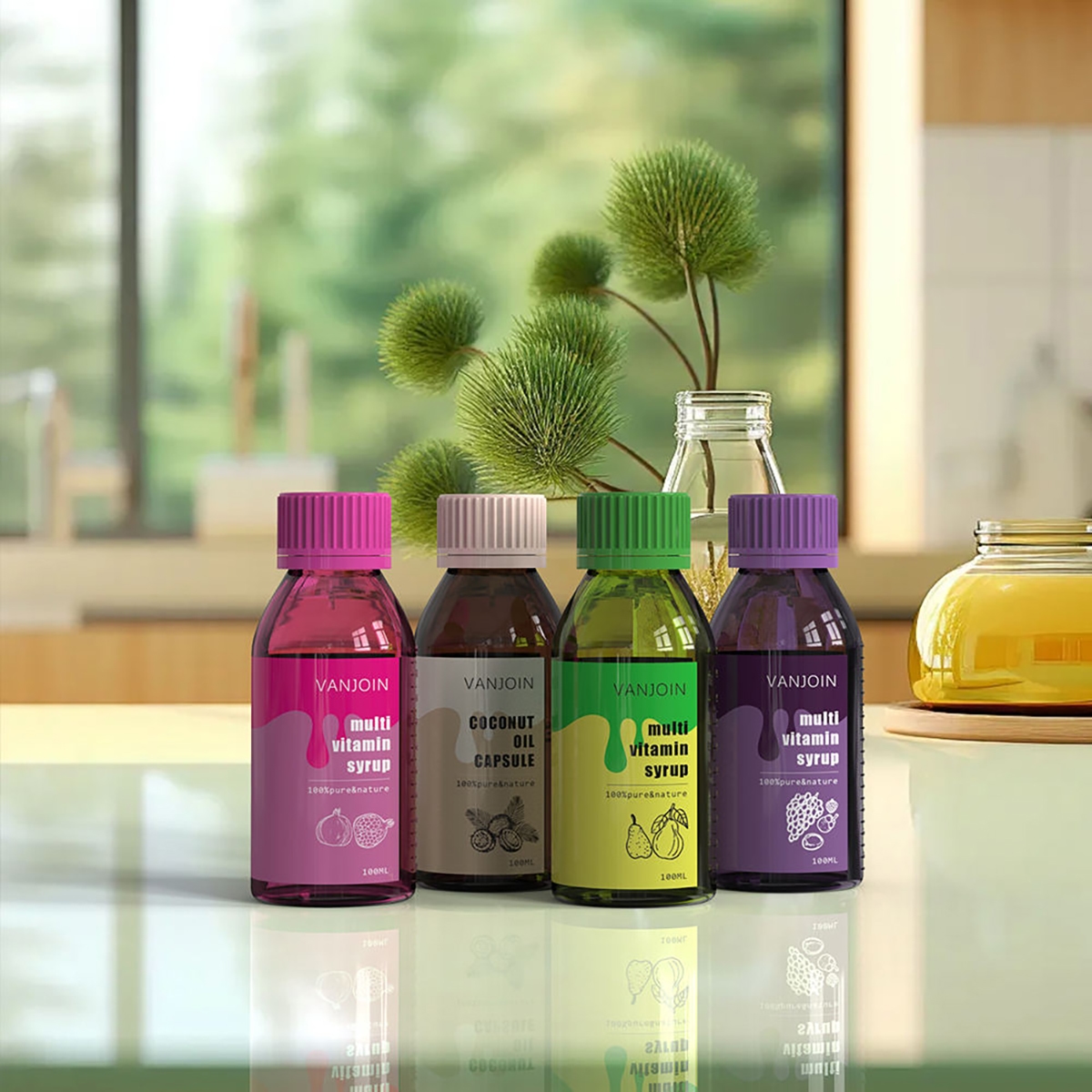
PET Green Masterbatch: The Sustainable Solution for Modern Plastics
In an era where sustainability is at the forefront of manufacturing, PET green masterbatch stands out as a vital innovation in the plastics industry. This guide explores everything you need to know about PET green masterbatch, its applications, benefits, and how it is transforming the way we think about color in plastic products. If you’re looking to understand how to incorporate sustainable practices into your plastic manufacturing processes, this article is essential reading.
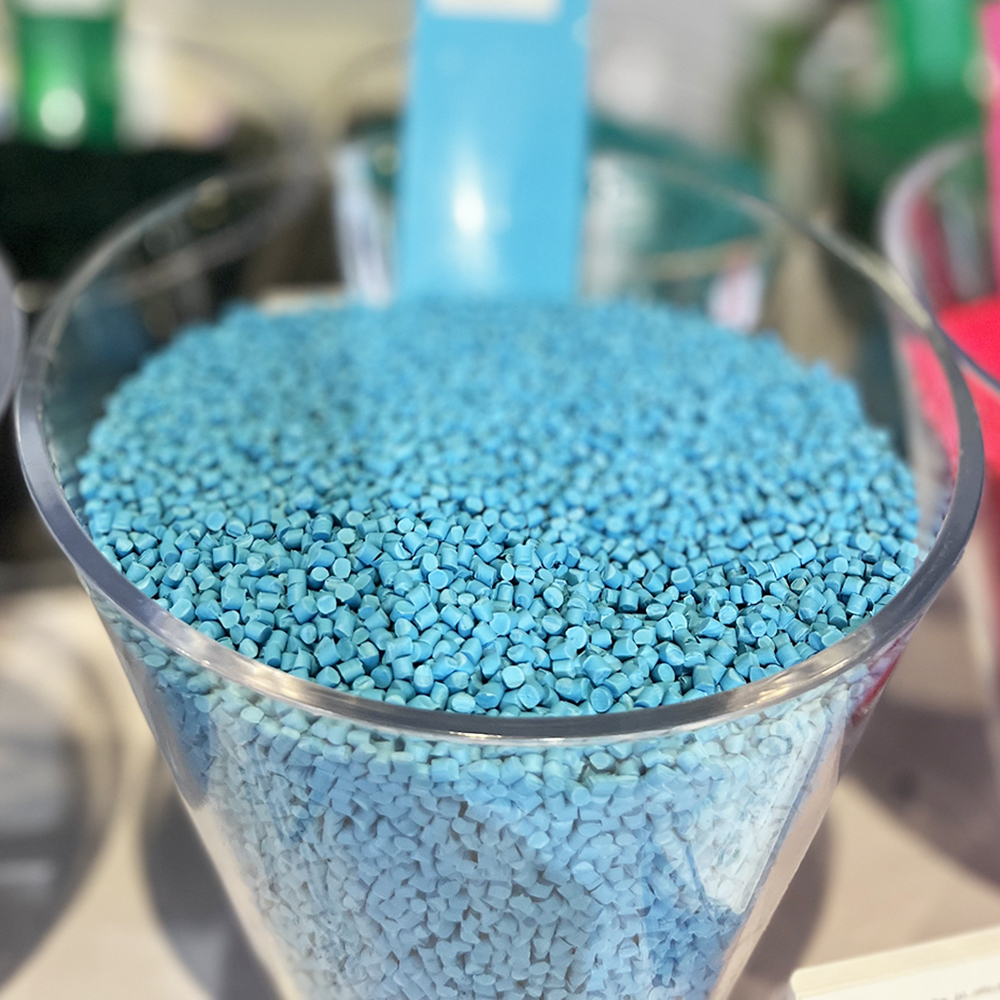
Masterbatch for Enhanced Safety: Safeguarding You and Your Products Throughout the Manufacturing Process
In the realm of plastic product manufacturing, safety stands as a paramount concern. Beyond its role in achieving consistent color and properties, masterbatch proves to be a crucial element in ensuring both your safety and the safety of the products you create.