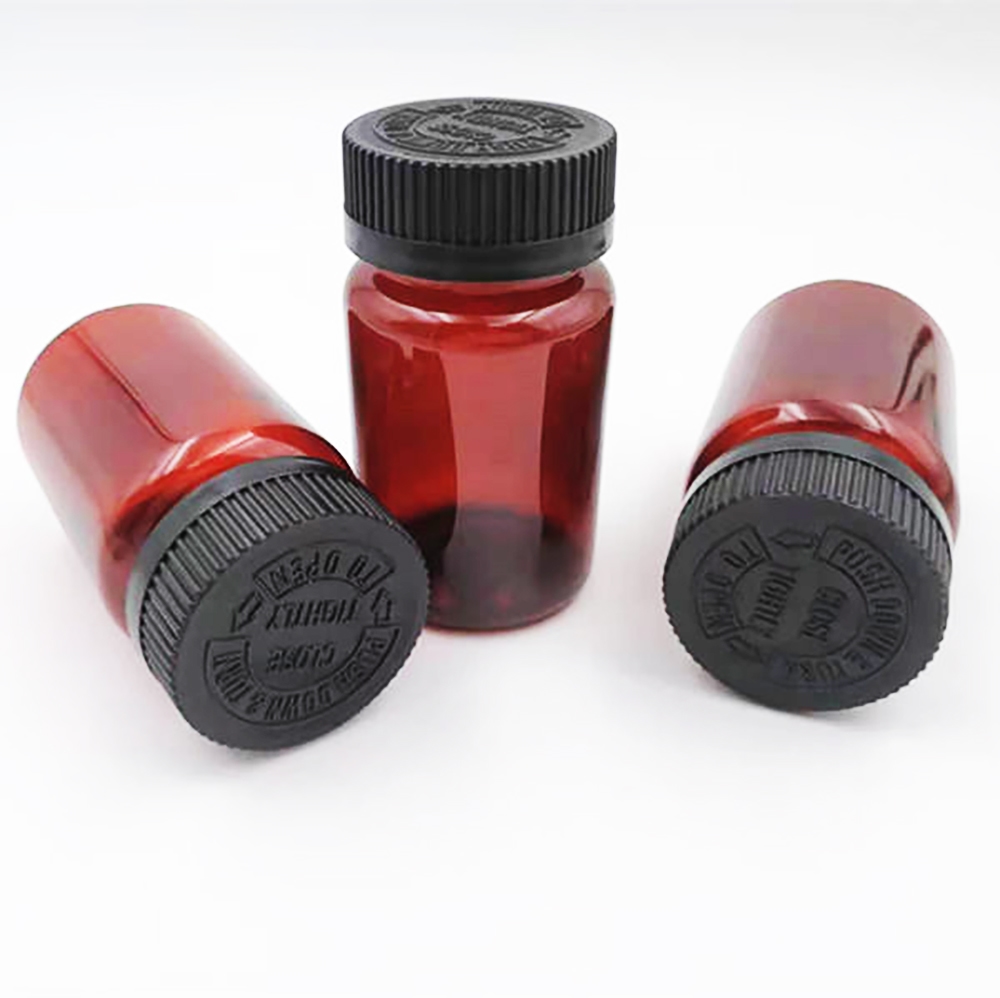
The Essential Guide to Amber Masterbatch in Pharmaceutical Packaging
Amber masterbatch plays a crucial role in the development and manufacturing of pharmaceutical packaging, particularly for PET (polyethylene terephthalate) materials.
A masterbatch is a concentrated blend of pigments and additives encapsulated into a polymer carrier through heat treatment and high-shear mixing in an extruder. Once mixed, the blend is cooled, cut, and formed into granules using a pelletizer. Producing masterbatch requires precision in the compounding process to ensure pigments and additives are uniformly and thoroughly mixed with the base polymer.
An alternative to using masterbatches is compounding materials from raw components on-site. However, compared to pure pigments, masterbatches require more storage space and have longer lead times. Additionally, masterbatches involve extra heat exposure for both the carrier and the additive, which is crucial for thermally unstable pigments. Despite these drawbacks, masterbatches, being premixed, help alleviate issues related to inadequate additive dispersion. The concentration of additives in the masterbatch is higher than in the final polymer, ensuring proper dispersion in the master resin. This process is similar to the use of ferroalloys in adding alloying elements to steel.
Masterbatches are highly concentrated, featuring high “let-down ratios,” meaning one tonne of natural polymer can be blended into a 25 kg bag of masterbatch. This dilution allows for precise dosing of expensive components. Solid masterbatches, being solvent-free, have a longer shelf life since the solvent in the polymer doesn’t evaporate. They generally contain 40-65% additives, although this can range from 15-80% in some cases. Liquid masterbatches enable highly accurate dosing and quick color changes between production runs.
White masterbatch is used in various applications, including lamination, coating, pipes, thermoforming, protective films, fibers, non-woven materials, blow molding, and injection molding. High-quality production capabilities include both outdoor and indoor grades of Titanium Dioxide (TiO2), which provides opacity by reflecting light through scattering, refraction, and diffraction. When light passes through TiO2 particles, enough light reflection makes the object appear opaque.
Benefits:
Black masterbatch is available in polyethylene, polypropylene, and universal carrier systems. Specially selected carbon blacks provide various properties from high jetness and UV protection to food contact approvals, offering economical options for coloration.
Features:
Color masterbatch significantly transforms plastic resins and their applications. They offer high-performance engineering thermoplastics, enhancing aesthetics, modifying properties, adding value, and defining form and function. Color masterbatches are integral in various sectors, from industrial equipment to home appliances, textiles to packaging. They provide thermal stability and color flexibility, essential for plastic products made with high-grade pigments. These masterbatches are used in processes such as insulation cables, injection molding, and blow molding of bottles.
Additive masterbatches help prevent degradation from heat, shear, UV radiation, and oxidation. They can also limit fire reactions, reduce product weight, and make synthetic surfaces easier to print or laser cut. Additionally, they help prevent static electricity buildup.
There has been significant growth in demand for well-finished plastic products. Differentiation in product and packaging design is of utmost importance in consumer markets. Rapid technological advancements and the development of exclusive new pigments have enabled us to support the market with innovative solutions for the plastics industry.
Key Characteristics:
In conclusion, masterbatch is essential for integrating pigments and additives into polymers efficiently. It enhances color, functionality, and performance across industries like packaging, automotive, and construction. With high concentration and precise dosing capabilities, masterbatches play a crucial role in advancing product quality and innovation in plastic manufacturing globally.
Learn more knowledge and trends in masterbatch industry from our blog.
Amber masterbatch plays a crucial role in the development and manufacturing of pharmaceutical packaging, particularly for PET (polyethylene terephthalate) materials.
Color masterbatches, also known as color concentrates for plastics, are plastic granules primarily employed for plastic coloring.
Masterbatch, a concentrated blend of pigments or additives, serves the purpose of coloring or enhancing the properties of plastic materials.
©2023. Masterbatch Manufacturer All Rights Reserved.
Our team will send back the best offer in 20 minutes.