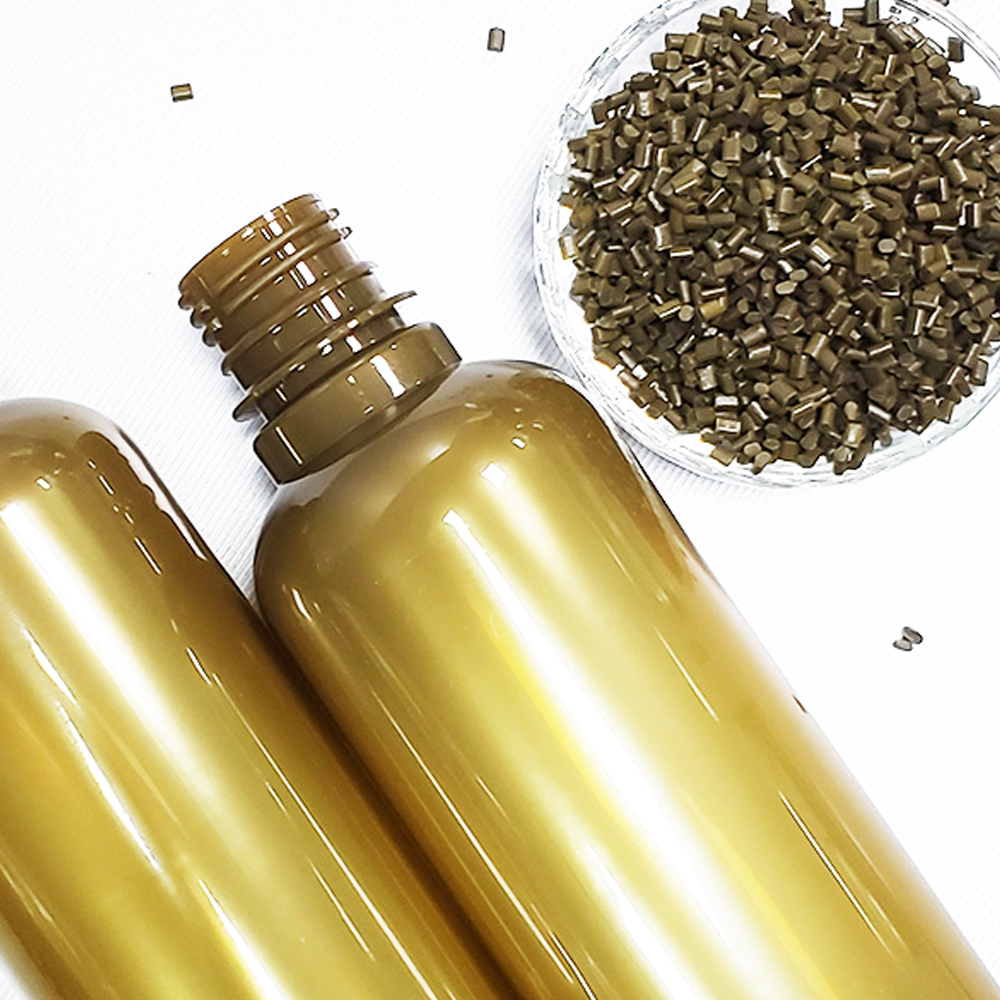
Unlocking Radiance: The Dynamic Role of Metallic Masterbatches in the Plastic Industry
Metallic masterbatches stand as versatile powerhouses within the realm of the plastic industry, wielding a transformative influence across various applications.
A crucial enhancement in the manufacturing process of plastic products is the incorporation of Antiblock Masterbatch, an innovation designed to tackle the age-old problem of plastic blocking, where layers of plastic adhere together. This phenomenon, known as blocking, can often make it arduous to separate individual layers.
Read on to gain insight into the realm of Antiblock Masterbatch, its significance, and the profound benefits it offers to plastic manufacturers across diverse industries.
Antiblock Masterbatch emerges as a vital additive in the production of plastic goods, universally applicable across a myriad of industries. This innovative masterbatch serves the dual purpose of mitigating air bubble formation and, more significantly, averting the blocking effect in plastic sheets, enhancing product quality and overall efficiency.
The primary conundrum that Antiblock Masterbatch addresses pertains to the formation of undesirable air bubbles during the manufacturing process. These tiny imperfections, if left unchecked, can evolve into significant flaws over time. The paramount issue, however, is the obstruction effect that arises when two smooth layers of plastic film adhere to one another, hindering their separation. Tosaf’s premium masterbatches represent the pinnacle of quality, bestowing enhanced durability and standards upon the manufactured products, empowering manufacturers to deliver excellence.
Certain polymer types, including polyolefins and polyesters, possess an innate propensity for blocking, leading to the unwelcome sticking of adjacent layers of polyolefin film. This occurrence results from the composition and rolling tension of the plastic film, manifesting during extrusion, conversion processes, or storage. Blocking can diminish the efficiency of packing operations, making bags challenging to open and rendering the separation of thermoformed trays in stacked configurations a cumbersome task.
Antiblock Masterbatch serves as the ultimate solution to this persistent problem, ensuring a smooth workflow by reducing surface adhesion in products composed of similar or dissimilar surfaces. The mechanism behind these masterbatches involves introducing a slight textural roughness to the surface, facilitating the effortless opening of bags and swift detachment of plastic sheets.
The primary objective of introducing Antiblock Masterbatch into the plastic production process is to counteract the sticking of plastic sheets, a prevalent issue particularly in films and plastic bags. Plastic manufacturers operating across diverse industries, neglecting to incorporate Antiblock Masterbatch, may face a decline in product quality and subsequent sales erosion due to this persistent problem. The impeccable quality of Tosaf’s Antiblock Masterbatch surmounts this issue effectively, resolving blocking problems and elevating plastic products to the pinnacle of efficiency.
The antiblock additive sector is on a robust growth trajectory, with projections suggesting an unprecedented surge over the next five years. The burgeoning demand can be attributed to the expanding packaging domain, notably in food, pharmaceuticals, and agriculture. Given the extensive use of plastic packaging across various industries, ensuring the delivery of top-quality products and packaging is of paramount importance.
The escalating use of plastics for both heavy and light packaging fuels the demand for Antiblock Masterbatch additives, pervading diverse applications within the packaging sector. The versatility of Antiblock Masterbatches transcends industry boundaries. From cosmetics and household products to consumables, food and beverage items, and more, plastics serve as a primary medium for packaging. As a result, the inclusion of Antiblock Masterbatch in the production process stands as an essential undertaking, guaranteeing that packaging and the products themselves, especially in the case of plastic sheets or bags, meet the highest contemporary quality standards.
In conclusion, Antiblock Masterbatch stands as a pivotal additive in the production of plastic goods across a wide spectrum of industries. Its primary function is to combat the blocking issue, preventing plastic sheets and bags from adhering to one another. As plastic products are seamlessly integrated into our daily lives, manufacturers continuously seek to enhance their offerings. By infusing their products with Antiblock Masterbatch, quality is instantaneously elevated, blocking issues are resolved, and customers can relish the finest product experience available.
Learn more knowledge and trends in masterbatch industry from our blog.
Metallic masterbatches stand as versatile powerhouses within the realm of the plastic industry, wielding a transformative influence across various applications.
Masterbatch, a concentrated blend of pigments or additives, serves the purpose of coloring or enhancing the properties of plastic materials.
Masterbatch refers to a solid additive used in the plastics industry to enhance properties or impart color to polymers. Essentially, it is a highly concentrated mixture of pigments or additives dispersed within a polymer carrier. This mixture is subjected to heat and high-shear mixing in an extruder, then cooled, cut, and transformed into granules or pellets through a pelletizer.
©2023. Masterbatch Manufacturer All Rights Reserved.
Our team will send back the best offer in 20 minutes.