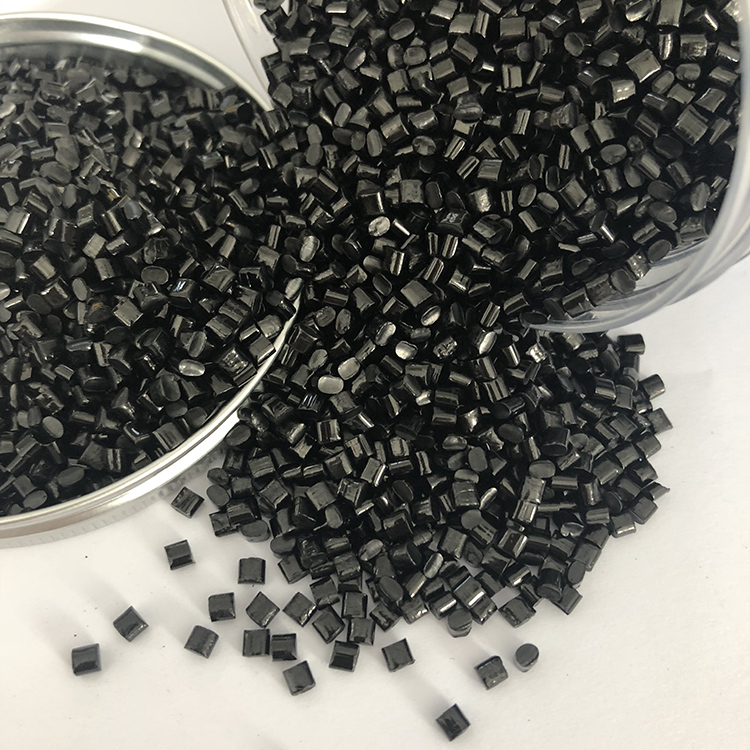
Mastering Core: The Art of PET Black Masterbatch Production
In the intricate world of coloring polyester fibers, the significance of a top-tier PET black masterbatch cannot be overstated. This specialized compound, designed for the meticulous task of infusing black hues into polyester fibers, sets the bar high.