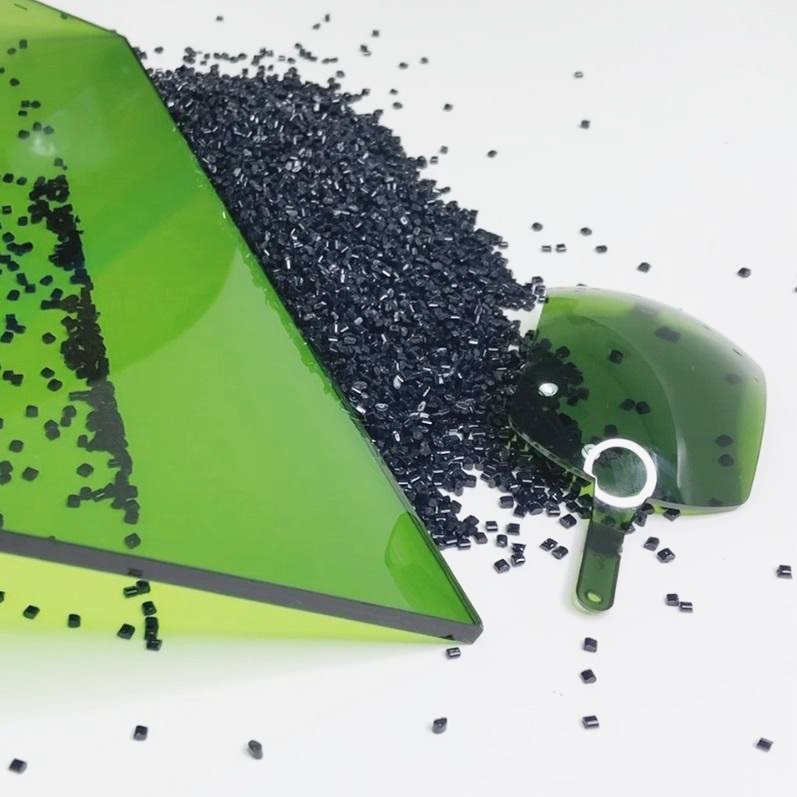
- +8615880211820
- [email protected]
- Tongan Industry Park, Xiamen
Leadership in Polyolefin Industry for PE Pipe Compounds
In the dynamic landscape of polyolefin industry, the demand for high-quality HDPE masterbatches is paramount, especially in applications such as PE-007, PE-009, and PE-015 pipe compounds. As a trailblazer in the field, we take pride in our extensive experience, spanning over 25 years, dedicated to crafting superior black and color HDPE masterbatches.
Our HDPE masterbatches are specially formulated for high-pressure gas and water pipes, boasting a guaranteed lifespan of over 50 years at maximum-rated pressure. The safety-critical nature of these masterbatches necessitates meticulous attention to detail, with high levels of dispersion and stringent quality control at the core of our manufacturing process.
We are recognized for our commitment to achieving unparalleled dispersion of particulate additives, along with uniform dispersion of primary and secondary antioxidants. Our dedication to quality is reflected in the classification and testing of our grades according to ISO 4427, EN 12201 (for drinking water applications), ISO 4437, and EN 1555 (for gas applications). This ensures an optimal balance of properties, including stress crack resistance, resistance to rapid crack propagation, creep resistance, and long-term strength.
Leveraging our deep industry knowledge, we present a comprehensive range of HDPE Pipe Black Masterbatches tailored to the diverse needs of our customers. Widely used in the extrusion of HDPE pipes, our masterbatches are available in various sizes, offering cost-effective solutions to our valuable clients.
For color masterbatches, the significance of vibrant and consistent color cannot be overstated, especially when applied to plastic products. Our meticulous approach ensures that the color is not just aesthetically pleasing but meets the highest standards of quality.
Diving into the realm of carrier-free masterbatch, we explore its unique attributes. The term “carrier-free” is relative, as there is no truly carrier-free masterbatch. Microcrystalline wax, dispersants, and other additives replace traditional carriers like resin. Our carrier-free black masterbatch utilizes microcrystalline wax as the main carrier, augmented with high-performance additives, achieving an impressive carbon black content of up to 70%.
Our specialized black masterbatch for blown film applications is a testament to our commitment to excellence. Crafted from high-quality resin, organic pigments, carbon black, and additives, our product ensures uniformity, heat resistance, and excellent dispersion. The resulting blown film products exhibit a superior level of blackness and brightness, with enhanced stability and resistance to cracking.
Cost-Efficiency Without Compromise: Our commitment to providing a high-performance HDPE pipe black masterbatch extends to ensuring cost-effectiveness without compromising on quality. We have strategically optimized our manufacturing processes to deliver superior products at a competitive price point.
Extended Service Life and Durability: The masterbatch is engineered to enhance the durability of HDPE pipes, ensuring a prolonged service life of over 50 years even under maximum-rated pressure. This not only contributes to the longevity of the pipes but also reduces the need for frequent replacements, resulting in significant cost savings over time.
Advanced Quality Control Measures: Rigorous quality control measures are implemented throughout the production process. We employ cutting-edge technology to monitor and maintain the quality of our masterbatch, ensuring that each batch meets the highest industry standards. This commitment to quality directly translates into reduced downtime and maintenance costs for end-users.
Tailored Dispersion for Optimal Performance: Achieving optimal dispersion of particulate additives is a hallmark of our HDPE pipe black masterbatch. The precise dispersion contributes to enhanced performance characteristics, including stress crack resistance, rapid crack propagation resistance, and overall structural integrity. This results in a reduction of potential failures and associated repair costs.
Compliance with Stringent Industry Standards: Our masterbatch grades are meticulously classified and tested according to ISO 4427, EN 12201, ISO 4437, and EN 1555 standards for drinking water and gas applications. This not only ensures regulatory compliance but also provides peace of mind to customers, knowing that our products meet the highest safety and quality benchmarks.
Versatility in Application: The versatility of our HDPE pipe black masterbatch extends to its compatibility with various materials, including PE, PP, PS, ABS, and more. This adaptability allows for a broad range of applications across different industries, providing customers with a flexible and cost-effective solution for their specific needs.
Efficient Color Masterbatch Processing: In addition to black masterbatch, our expertise extends to color masterbatch processing. We understand the importance of vibrant and consistent color in plastic products. Our color masterbatch not only meets high aesthetic standards but is also processed efficiently, minimizing waste and contributing to overall cost savings.
Customer-Centric Sizing Options: Recognizing the diverse needs of our customers, we offer a range of sizing options for our HDPE pipe black masterbatch. This customer-centric approach allows clients to select the appropriate size for their specific extrusion requirements, promoting efficiency and cost-effectiveness in the manufacturing process.
Environmentally Responsible Practices: Our commitment to environmental responsibility is reflected in the non-toxic and environmentally-friendly nature of our masterbatch. This not only aligns with sustainable practices but also positions our product as a responsible and cost-effective choice for eco-conscious industries.
Collaborative Customer Support: Our dedication to customer satisfaction extends beyond product quality to encompass collaborative customer support. We work closely with our clients to understand their unique requirements and offer tailored solutions that maximize performance while optimizing costs.
In summary, our High Performance HDPE Pipe Black Masterbatch not only stands out for its exceptional quality and performance but also for its cost-effective features, making it a prudent choice for industries seeking a reliable and budget-friendly solution for their HDPE pipe applications.
In conclusion, our High Performance HDPE Pipe Black Masterbatch stands as a testament to our commitment to quality, longevity, and versatility in meeting the stringent demands of the polyolefin industry. With a legacy built on experience and innovation, we continue to pave the way for excellence in the world of HDPE masterbatches.
Our masterbatches find a multitude of applications across diverse industries. Whether in plastics, textiles, or various manufacturing processes, our masterbatches play a pivotal role in enhancing product quality and performance. With customizable formulations, they offer color consistency, UV protection, flame resistance, and more, making them the go-to solution for countless applications. From automotive parts to packaging materials, our masterbatches are the trusted choice for achieving superior results across a wide spectrum of industries.
Our custom masterbatches are designed to match specific polymers, ensuring optimal performance when incorporated into your selected material. We have the capability to produce masterbatches suitable for a variety of polymers mentioned below, and many more. If you’re working with a material that isn’t listed here, please don’t hesitate to reach out to our knowledgeable technical team to explore the possibility of meeting your specific needs.
Low Density Polyethylene – Somewhat more translucent than HDPE and considerably more pliable, primarily employed in flexible packaging, tote bags, pliable tubing, film applications, and similar uses. Like HDPE, it has limited transparency characteristics. It exhibits outstanding chemical resistance to alcohols, acids, and alkalis but has restricted resistance to hydrocarbon solvents and mineral oils. Prolonged exposure to UV radiation can initiate degradation.
High-Density Polyethylene – Featuring a somewhat milky-white appearance, this material finds wide application in rigid bottle packaging, injection-molded caps and closures, crates, and more. Its natural opacity can limit the degree of transparency attainable. HDPE exhibits superior chemical and solvent resistance when compared to LDPE.
PPCO Random & PPHO – A polymer with moderate clarity, employed in the production of caps and closures. It is also utilized for crafting household items, buckets, toys, and storage containers. Polypropylene offers flexibility without significant limitations on color or special effects. Random copolymer boasts greater clarity compared to homopolymer and is better suited for creating translucent shades.
PPCO Block – Similar to PPCO but enhanced for increased impact resistance. An additive renders the polymer white, resulting in high opacity. This characteristic may limit the achievable transparency.
Polyethylene Terephthalate (PET) – Polyester materials exhibit robust mechanical strength along with excellent chemical resistance and barrier properties. PET is frequently chosen for the production of carbonated beverage containers. Moreover, polyester can be spun and employed in textile manufacturing for clothing. PET is highly transparent, making it an excellent choice for translucent packaging, although a subtle hint of “yellowing” may impact extremely light tints.
Polybutylene Terephthalate – A crystalline thermoplastic engineering polymer frequently employed as an insulating material within the electronics sector. This substance belongs to the polyester category, showcasing a remarkable equilibrium of attributes and processing qualities.
General Purpose Polystyrene – Exhibiting a glass-clear appearance but possessing minimal impact resistance, this material finds its primary application in CD cases. Its notable clarity renders it suitable for creating translucent hues, although an occasional violet tint may be discernible.
High Impact Polystyrene – Derived from GPPS by incorporating an impact-enhancing agent to boost its resistance to impacts. This added component results in the polymer becoming white, and different formulations provide varying degrees of opacity. Typically employed in the fabrication of game pieces, toys, and similar items. Its pronounced whiteness can pose challenges when aiming for translucent coloration. Specialized alternatives like K-Resin and Styrolux are accessible in the market to attain the same level of translucency as GPPS.
Acrylonitrile Butadiene Styrene (ABS) – A more robust iteration of High Impact Polystyrene (HIPS) employed in high-value components. ABS exhibits greater durability compared to HIPS-made components, although it encounters similar challenges when attempting to achieve translucent colorations. Just like HIPS, ABS offers specialized translucent variants. Owing to its durability, ABS is commonly used in crafting casings for power tools.
Polyamide (6, 66) – Nylon represents a versatile grade extensively employed in mechanical construction and maintenance. Its popularity stems from its excellent blend of mechanical strength, rigidity, mechanical damping characteristics, and effective electrical insulation capabilities. Consequently, nylon is a preferred material for manufacturing electrical enclosures. PA66 serves as a common alternative to metal across diverse applications, with its chemical and physical attributes closely resembling those of PA6. PA6 exhibits superior impact resistance and resistance to solvents, albeit with a heightened susceptibility to moisture absorption.
Styrene Acrylonitrile Copolymer – Possessing transparency and outstanding chemical and heat resistance, SAN also boasts good rigidity, tensile strength, and flexural strength. Thanks to its high-gloss finish, SAN is commonly chosen for cosmetic packaging purposes. However, achieving light tint colors with SAN can be challenging due to the violet dyestuffs inherent in the material, which are utilized to enhance its visual appearance during manufacturing.
Polyethylene Terephthalate Glycol – PET with the incorporation of glycol. This glycol addition enhances flow properties but diminishes strength. PETG can be extruded to create bottles and can be formed into sheets for producing ‘blister’ style packaging.
Thermoplastic Elastomer (TPE) or Thermoplastic Polyurethane (TPU) – TPU finds diverse uses in applications such as automotive instrument panels, caster wheels, power tools, medical devices, as well as various extruded film, sheet, and profile applications. TPEs are employed across a wide range of applications in industries spanning automotive, medical, construction, electrical, appliances, packaging, and industrial sectors.
Frequently asked questions about our masterbatch
©2023. Masterbatch Manufacturer All Rights Reserved.
Our team will send back the best offer in 20 minutes.