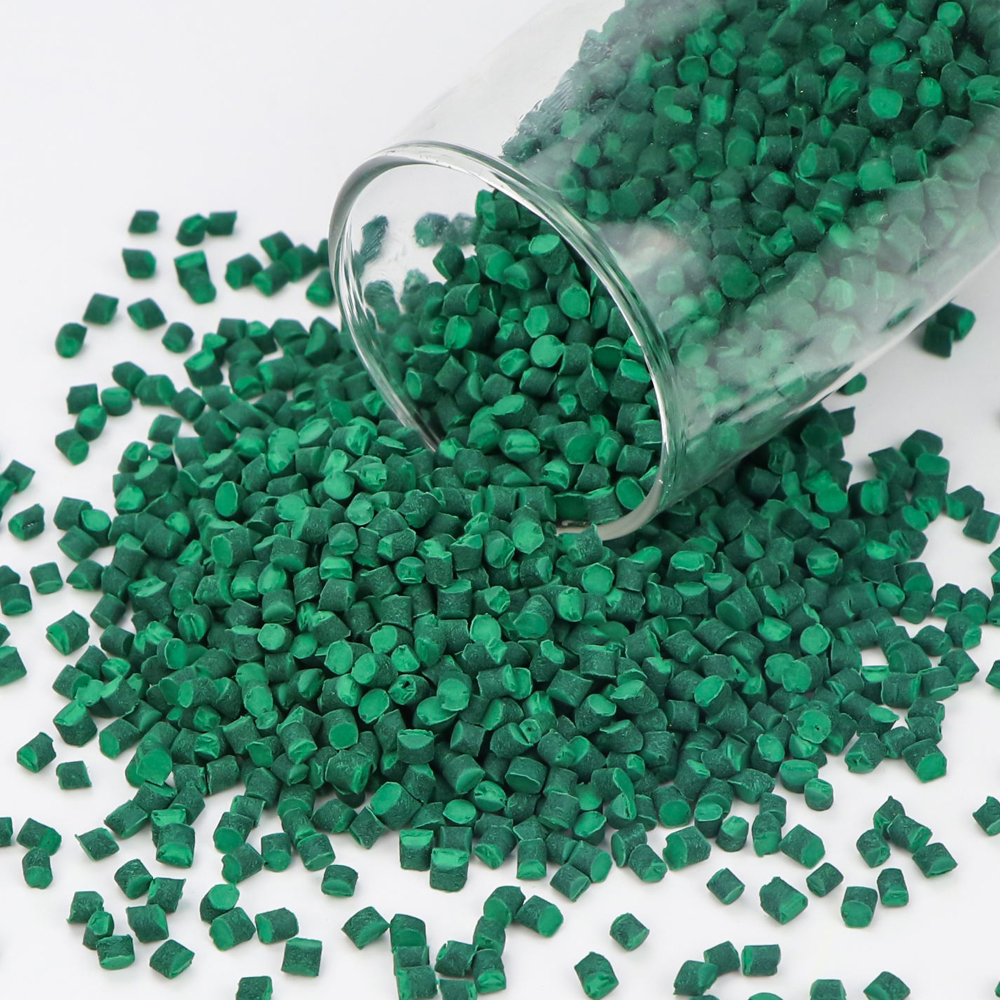
- +8615880211820
- [email protected]
- No.67, Tongan Industry Park, Xiamen
Polypropylene (PP) has long been recognized for its exceptional processing characteristics, making it a preferred material in various industries. Its good fluidity at melting temperatures and excellent molding performance have enabled a broad range of applications, from automotive components to household appliances. In recent times, there has been a significant leap in the development of modified plastic raw material, particularly in the realm of flame-retardant PP pellets. This article explores the process characteristics of PP and delves into the innovative features of V0 flame-retardant polypropylene pellets.
PP boasts impressive fluidity at melting temperature and favorable molding performance. Notably, the viscosity of PP melt decreases significantly with the increase in shear rate, making it less affected by temperature. The degree of crystallization in PP is primarily determined by mold temperature, ideally controlled within the range of 30-50°C. PP’s ability to pass through narrow mold gaps is attributed to its unique characteristics. During the melting process, PP absorbs a considerable amount of heat of fusion, resulting in products being hotter after ejection from the mold. Unlike some materials, PP does not require drying during processing, and its shrinkage rate and crystallinity are lower than that of PE.
PP has been a mainstay in fiber manufacturing due to its coloring ability, abrasion resistance, chemical resistance, and economic viability. It finds applications in the automotive industry, appliances, and various consumer goods. Injection molded products, including containers, sealers, automotive components, household products, toys, and other consumer and industrial items, constitute a significant market for PP homopolymers.
The recent focus on flame-retardant PP compounds has led to the development of V0 flame-retardant polypropylene pellets. These pellets are designed to meet the stringent flame-retardant requirements for applications in electrical work, especially in commercial and industrial settings. The flame-retardant systems commonly used include bromine-based, phosphorus-based, and halogen-free expansion systems. As environmental and health concerns rise, there is a noticeable shift towards halogen-free flame retardants, positioning them as the new mainstream in flame-retardant technology.
V0 flame-retardant polypropylene pellets find diverse applications in various industries, including:
Conclusion: The continuous advancements in flame-retardant polypropylene pellets, particularly in the V0 category, signify a major breakthrough in enhancing the safety and performance of industrial products. With applications ranging from auto parts to electronic appliances, these pellets are poised to play a pivotal role in ensuring the reliability and durability of a wide array of consumer and industrial goods. As technology continues to evolve, flame-retardant PP plastics are expected to witness even greater adoption across diverse industries.
Our masterbatches find a multitude of applications across diverse industries. Whether in plastics, textiles, or various manufacturing processes, our masterbatches play a pivotal role in enhancing product quality and performance. With customizable formulations, they offer color consistency, UV protection, flame resistance, and more, making them the go-to solution for countless applications. From automotive parts to packaging materials, our masterbatches are the trusted choice for achieving superior results across a wide spectrum of industries.
Our custom masterbatches are designed to match specific polymers, ensuring optimal performance when incorporated into your selected material. We have the capability to produce masterbatches suitable for a variety of polymers mentioned below, and many more. If you’re working with a material that isn’t listed here, please don’t hesitate to reach out to our knowledgeable technical team to explore the possibility of meeting your specific needs.
Low Density Polyethylene – Somewhat more translucent than HDPE and considerably more pliable, primarily employed in flexible packaging, tote bags, pliable tubing, film applications, and similar uses. Like HDPE, it has limited transparency characteristics. It exhibits outstanding chemical resistance to alcohols, acids, and alkalis but has restricted resistance to hydrocarbon solvents and mineral oils. Prolonged exposure to UV radiation can initiate degradation.
High-Density Polyethylene – Featuring a somewhat milky-white appearance, this material finds wide application in rigid bottle packaging, injection-molded caps and closures, crates, and more. Its natural opacity can limit the degree of transparency attainable. HDPE exhibits superior chemical and solvent resistance when compared to LDPE.
PPCO Random & PPHO – A polymer with moderate clarity, employed in the production of caps and closures. It is also utilized for crafting household items, buckets, toys, and storage containers. Polypropylene offers flexibility without significant limitations on color or special effects. Random copolymer boasts greater clarity compared to homopolymer and is better suited for creating translucent shades.
PPCO Block – Similar to PPCO but enhanced for increased impact resistance. An additive renders the polymer white, resulting in high opacity. This characteristic may limit the achievable transparency.
Polyethylene Terephthalate (PET) – Polyester materials exhibit robust mechanical strength along with excellent chemical resistance and barrier properties. PET is frequently chosen for the production of carbonated beverage containers. Moreover, polyester can be spun and employed in textile manufacturing for clothing. PET is highly transparent, making it an excellent choice for translucent packaging, although a subtle hint of “yellowing” may impact extremely light tints.
Polybutylene Terephthalate – A crystalline thermoplastic engineering polymer frequently employed as an insulating material within the electronics sector. This substance belongs to the polyester category, showcasing a remarkable equilibrium of attributes and processing qualities.
General Purpose Polystyrene – Exhibiting a glass-clear appearance but possessing minimal impact resistance, this material finds its primary application in CD cases. Its notable clarity renders it suitable for creating translucent hues, although an occasional violet tint may be discernible.
High Impact Polystyrene – Derived from GPPS by incorporating an impact-enhancing agent to boost its resistance to impacts. This added component results in the polymer becoming white, and different formulations provide varying degrees of opacity. Typically employed in the fabrication of game pieces, toys, and similar items. Its pronounced whiteness can pose challenges when aiming for translucent coloration. Specialized alternatives like K-Resin and Styrolux are accessible in the market to attain the same level of translucency as GPPS.
Acrylonitrile Butadiene Styrene (ABS) – A more robust iteration of High Impact Polystyrene (HIPS) employed in high-value components. ABS exhibits greater durability compared to HIPS-made components, although it encounters similar challenges when attempting to achieve translucent colorations. Just like HIPS, ABS offers specialized translucent variants. Owing to its durability, ABS is commonly used in crafting casings for power tools.
Polyamide (6, 66) – Nylon represents a versatile grade extensively employed in mechanical construction and maintenance. Its popularity stems from its excellent blend of mechanical strength, rigidity, mechanical damping characteristics, and effective electrical insulation capabilities. Consequently, nylon is a preferred material for manufacturing electrical enclosures. PA66 serves as a common alternative to metal across diverse applications, with its chemical and physical attributes closely resembling those of PA6. PA6 exhibits superior impact resistance and resistance to solvents, albeit with a heightened susceptibility to moisture absorption.
Styrene Acrylonitrile Copolymer – Possessing transparency and outstanding chemical and heat resistance, SAN also boasts good rigidity, tensile strength, and flexural strength. Thanks to its high-gloss finish, SAN is commonly chosen for cosmetic packaging purposes. However, achieving light tint colors with SAN can be challenging due to the violet dyestuffs inherent in the material, which are utilized to enhance its visual appearance during manufacturing.
Polyethylene Terephthalate Glycol – PET with the incorporation of glycol. This glycol addition enhances flow properties but diminishes strength. PETG can be extruded to create bottles and can be formed into sheets for producing ‘blister’ style packaging.
Thermoplastic Elastomer (TPE) or Thermoplastic Polyurethane (TPU) – TPU finds diverse uses in applications such as automotive instrument panels, caster wheels, power tools, medical devices, as well as various extruded film, sheet, and profile applications. TPEs are employed across a wide range of applications in industries spanning automotive, medical, construction, electrical, appliances, packaging, and industrial sectors.
Frequently asked questions about our masterbatch
©2023. Masterbatch Manufacturer All Rights Reserved.
Our team will send back the best offer in 20 minutes.