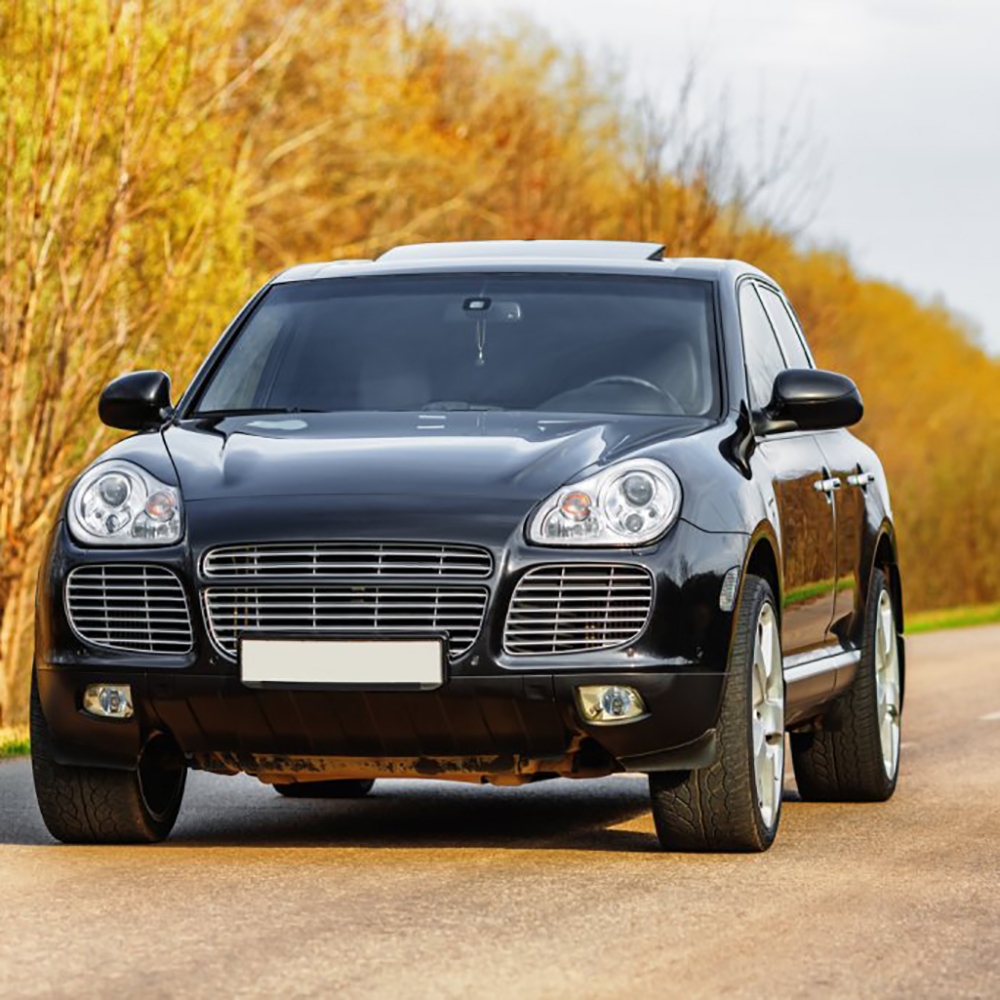
Masterbatch: Um guia completo para aprimorar a fabricação de plástico
Na fabricação moderna de plástico, o masterbatch desempenha um papel crítico na obtenção das propriedades desejadas e apelo estético em produtos acabados. Seja usado para conferir cores vibrantes, melhorar o desempenho do material ou atender aos padrões específicos da indústria, o masterbatch é uma solução indispensável para obter resultados consistentes e de alta qualidade.