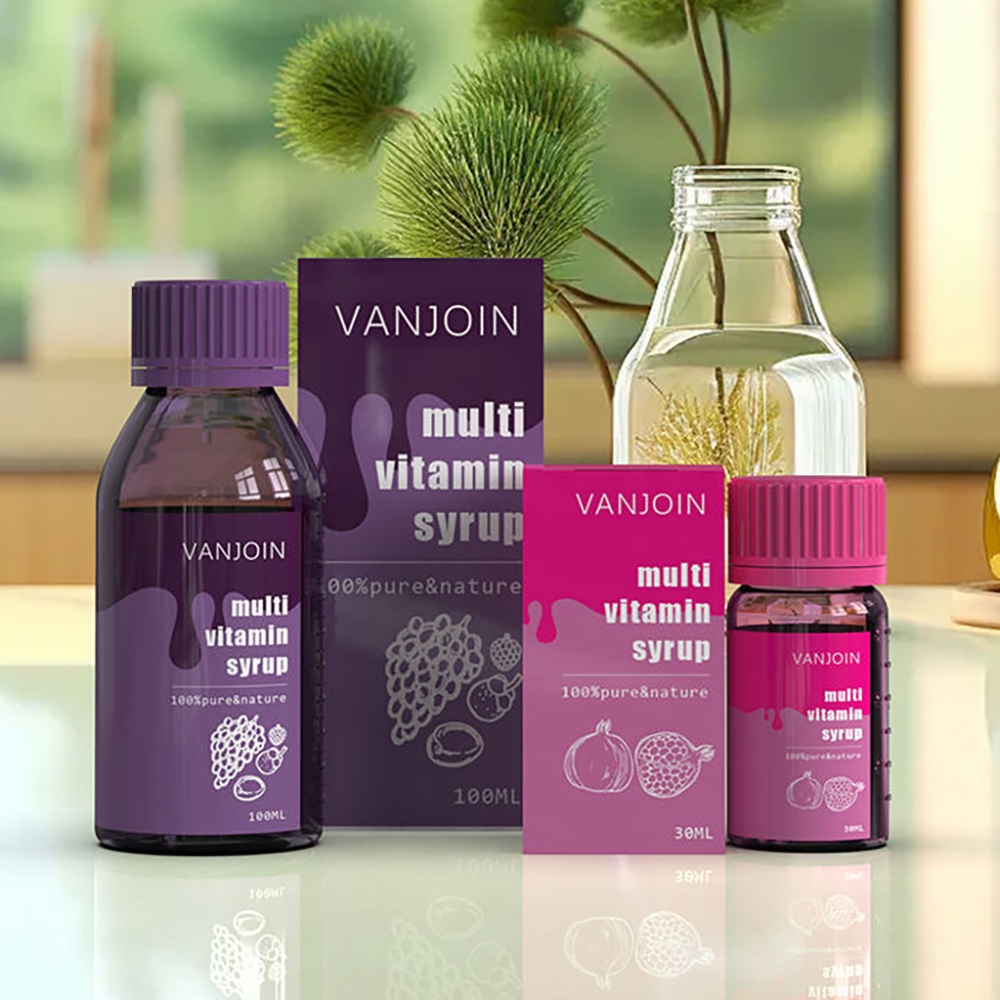
Hướng dẫn tối ưu về Masterbatch màu tím PET: Nâng cao chất lượng sản phẩm nhựa của bạn
Trong thế giới nhựa, màu sắc và chất lượng là tối quan trọng. Hạt nhựa màu tím PET là một bước ngoặt đối với các nhà sản xuất muốn nâng cao sản phẩm của mình bằng màu sắc rực rỡ và hiệu suất vượt trội. Bài viết này đi sâu vào sự phức tạp của hạt nhựa màu tím, các ứng dụng của nó và lý do tại sao nó lại cần thiết cho quy trình sản xuất nhựa của bạn.