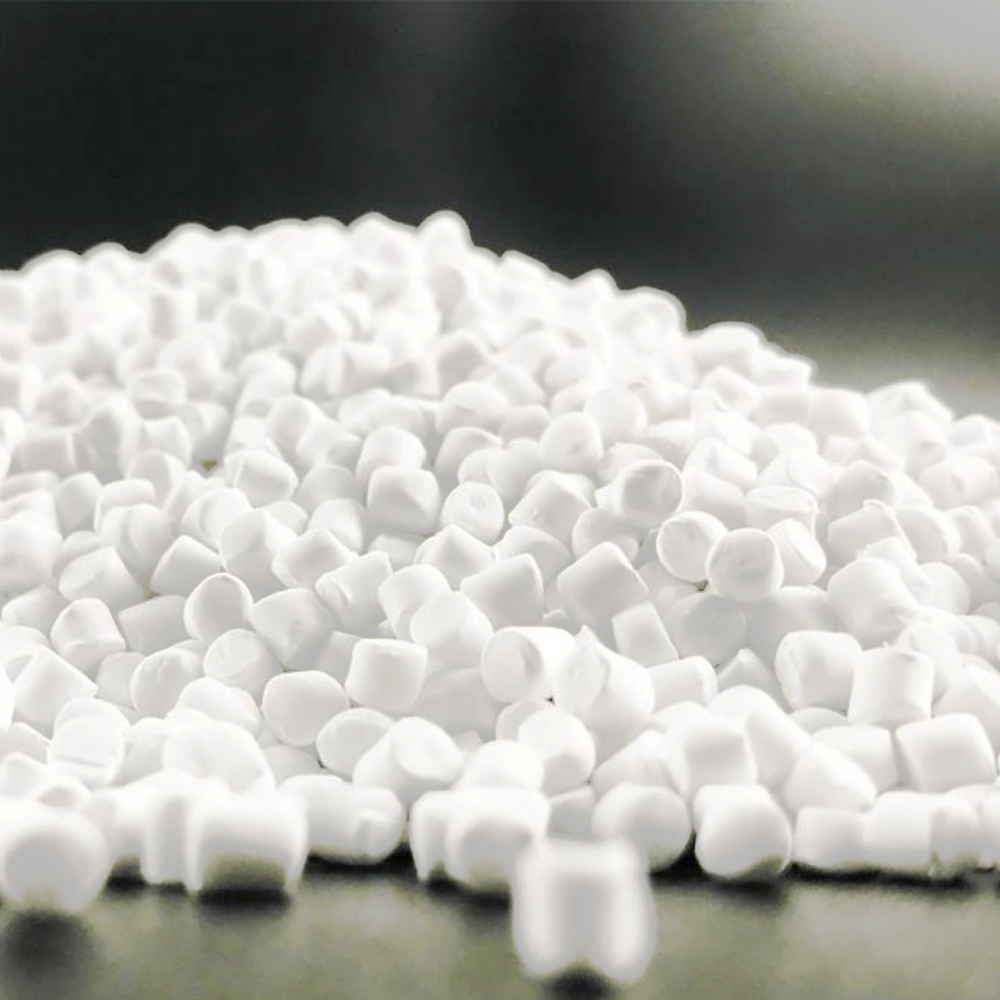
Odor Neutralizer Masterbatches: The Pinnacle of Odor Control Solutions
Odor Neutralizer Masterbatches represent a cutting-edge solution designed to absorb and minimize unwanted odors emitted by recycled polymers and products exposed to constant humidity and moisture.