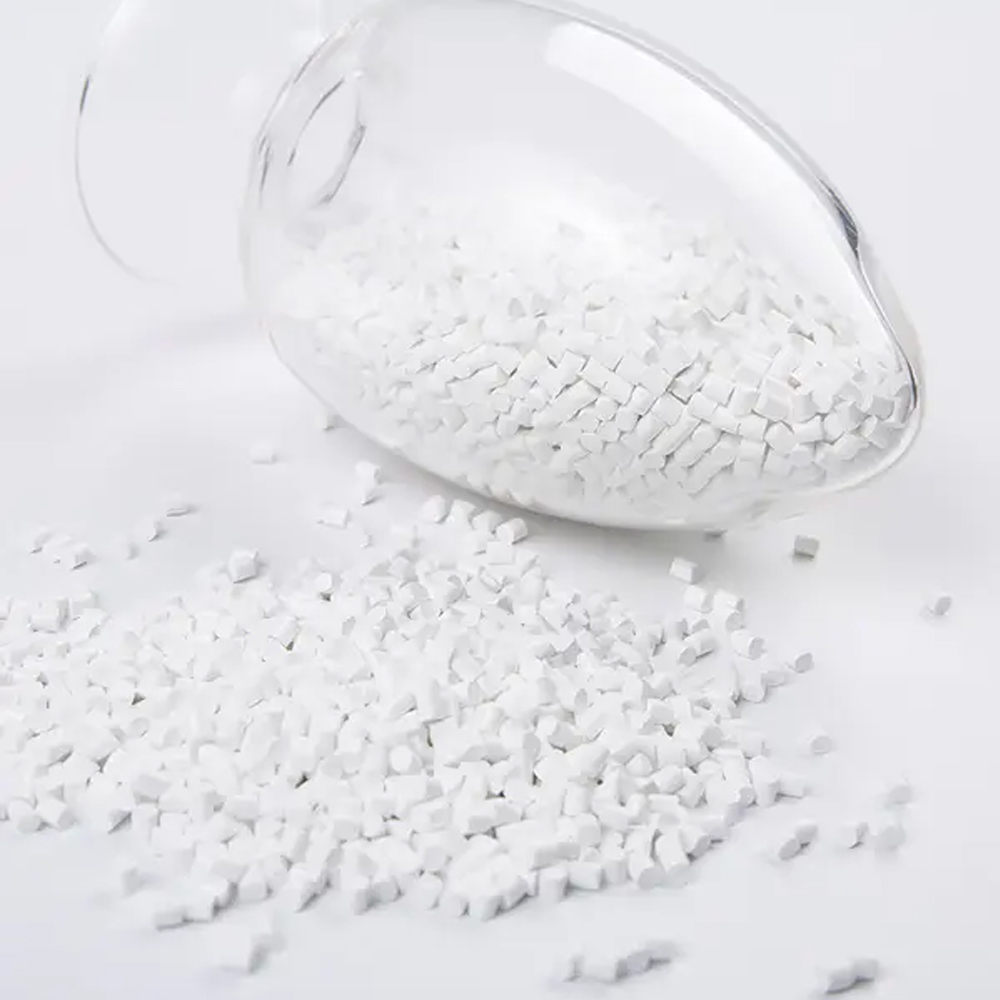
Applications of Masterbatch: Exploring a Range of Industries
For businesses operating in sectors such as packaging, automotive, consumer goods, construction, or textiles, familiarity with Masterbatch is likely crucial in the manufacturing process.
These masterbatches consist of two primary constituents: the colorants and a polymer-specific carrier resin. Some specialized formulations may also incorporate processing additives like zinc, oil, wax, etc., and possibly fillers, typically calcium carbonate powders. This type of masterbatch is widely utilized in numerous aspects of daily life, boasting a wide range of applications. Have you ever wondered about the production process behind them? This article sheds light on this subject.
Before delving deeper into the composition of color masterbatches, let’s clear up some misconceptions prevalent in the plastic industry. Firstly, it’s essential to understand that color masterbatch isn’t composed solely of pure pigment or colorants. On the contrary, it contains carrier resins, making it less concentrated than the original colorants. These colorants can be categorized into three sub-groups: organic dyes, organic pigments, and inorganic pigments. For black and white masterbatches, which are the most commonly used color concentrates for plastics, the intense color typically arises from carbon black (P or HAF) and TiO2 (rutile/anatase), respectively.
Color plays a crucial role in enhancing design and pleasing the eye. The significance of colors in our lives cannot be denied. That’s why efforts are made to provide more color choices for most commercial products. In the realm of plastics, color masterbatch was developed for this very purpose – infusing vibrancy and dramatic color into plastic products and their various applications. Some of the benefits our products offer include ease of use, high color concentration, excellent color quality, color stability, exceptional color dispersion capability, resistance to light fading and heat, cost savings (compared to direct pigment usage), reduced processing time (easy direct mixing during processing), and minimal environmental impact. Color masterbatch is now widely used across a range of industries, including textiles, automotive, packaging, construction, electronics, and electrical, among others.
Color masterbatch slightly differs from colored resins, even though they share major ingredients. While color masterbatch may contain 20 – 75% colorants (the actual dyeing agents, which can be in powder or liquid pigment form), colored resins used in plastic product manufacturing contain significantly lower amounts of these colorants. The recommended usage dose for most masterbatch manufacturers (including our factory) falls within the range of 2 to 10%.
To meet global market requirements, color concentrates for plastics must adhere to several criteria. These include uniform granule size (approximately 3mm), stable quality with excellent color dispersion, and the use of high-quality ingredients with 100% virgin resin. Such masterbatches help end products achieve a smooth surface with good printability and durability. Our factory is equipped with 2 production lines for White masterbatch, 7 production lines for black masterbatch, and multiple production lines for color masterbatch and additive masterbatch.
The production of each type of color masterbatch, tailored to the desired color and special effects, follows a meticulously controlled process at our company. We take into account various factors, including viscosity, melting temperature, environmental conditions, chemical resistance, and FDA suitability, to develop specific recipes that meet all customer requirements, even the most demanding ones. Our color range is based on various coloring systems, such as RAL and PANTONE, each offering unique effects, properties, and benefits.
In conclusion, color masterbatch, those vibrant and essential components in the world of plastics, offers a kaleidoscope of benefits to various industries and applications. These color concentrates bring life, appeal, and versatility to plastic products, enhancing their visual appeal and functionality. By understanding the composition of color masterbatch and its distinctions from colored resins, we gain insight into the art and science behind this essential manufacturing process.
High-quality color masterbatch meets stringent criteria, ensuring uniformity, stability, and top-notch performance. It is a testament to innovation and precision in the field of plastic production. Our factory takes pride in delivering world-class color masterbatch that caters to the unique demands of our customers, be it for aesthetics, functionality, or environmental considerations.
As we continue to explore and develop new color effects and properties, we unlock endless possibilities for the use of color masterbatch in diverse industries. The future of plastics is colorful, and it’s a future where our products play a pivotal role.
Whether it’s textiles, automotive, packaging, construction, electronics, or countless other sectors, color masterbatch adds the hues that make life more vivid and products more versatile. With its myriad advantages and applications, color masterbatch truly exemplifies the saying: “Life is better in color.”
Learn more knowledge and trends in masterbatch industry from our blog.
For businesses operating in sectors such as packaging, automotive, consumer goods, construction, or textiles, familiarity with Masterbatch is likely crucial in the manufacturing process.
Xinwancai Masterbatches stands at the forefront globally for PET Masterbatches, a product line highly sought after. These masterbatches boast a wide spectrum of vibrant and luxurious colors, often unattainable through conventional pigment or dye techniques.
Masterbatch, a potent blend of pigments and additives, serves as a vital ingredient in the plastic industry. White masterbatch, specifically, is a plastic enhancer tasked with bestowing a brilliant, white hue to plastic products.
©2023. Masterbatch Manufacturer All Rights Reserved.
Our team will send back the best offer in 20 minutes.