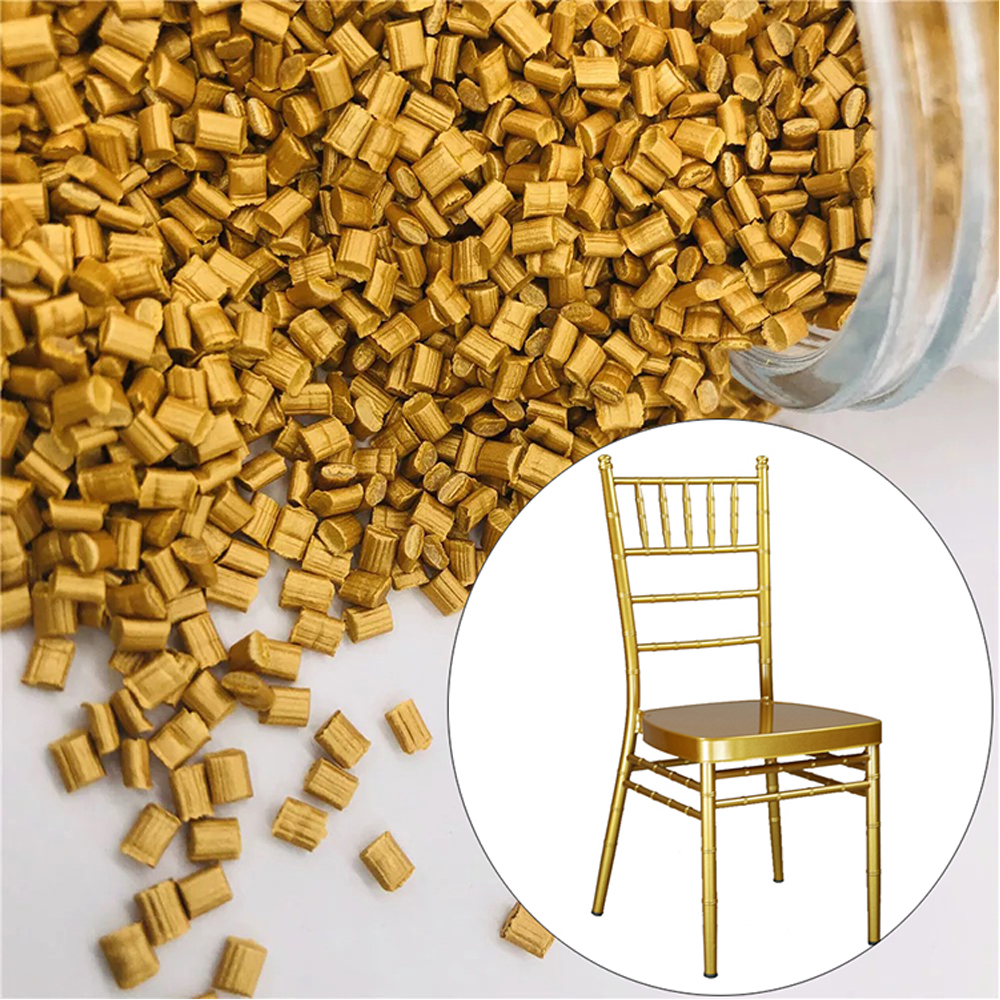
- +8615880211820
- [email protected]
- No.67, Tongan Industry Park, Xiamen
Introduction: SIS, or Styrene-Isoprene-Styrene, block copolymer stands as a high-performance thermoplastic elastomer renowned for its unique combination of attributes. With a balance of high strength, low hardness, and low viscosity, SIS polymers offer exceptional versatility in various applications. Derived from styrene and isoprene, these polymers exhibit superior performance and eco-friendly properties, making them indispensable in industries ranging from adhesive manufacturing to asphalt modification.
SIS polymers emulate the properties of vulcanized rubber without the need for vulcanization, providing manufacturers with enhanced flexibility and efficiency in processing. Their superior thermal stability and adhesion further contribute to their appeal in diverse applications. Notably, SIS is environmentally friendly, non-toxic, and recyclable, aligning with modern sustainability goals. Additionally, the use of solvents is generally unnecessary, streamlining production processes and minimizing environmental impact.
Item | Grade and Typical Value | ||||||||||
HC-9151 | HC-9152 | HC-9153 | HC-9161 | HC-9162 | HC-9163 | HC-9220 | HC-9291 | HC-9325 | HC-9360 | HC-9600 | |
Structure | Line | Line | Line | Line | Line | Line | Line | Line | Line | Hybrid | Line |
Polystyrene Content, wt% | 15 | 16 | 15 | 16 | 16 | 15 | 25 | 29 | 25 | 14 | 42 |
Diblock Content, wt% | <1 | 16.5 | 20 | 50 | 50 | 40 | 25 | 18 | 25 | 12 | <1 |
Melt Flow Rate g/10min(200℃/5kg) | 10 | 10 | 15 | 12 | 20 | 25 | 27 | 10 | 14 | 10 | 40 |
25%Toluene Solution Viscosity mPa.s | 1500 | 1100 | 1000 | 880 | 700 | 800 | 260 | 350 | 300 | 1500 | 120 |
Ash % | 0.1 | 0.1 | 0.1 | 0.1 | 0.1 | 0.1 | 0.1 | 0.1 | 0.1 | 0.1 | 0.05 |
Volatile Matter, wt% | 0.5 | 0.5 | 0.5 | 0.5 | 0.5 | 0.5 | 0.5 | 0.5 | 0.5 | 0.5 | 0.4 |
Density | 0.93 | 0.925 | 0.92 | 0.92 | 0.92 | 0.92 | 0.93 | 0.94 | 0.93 | 0.93 | 0.95 |
Tensile Strength ,ASTM D412, Mpa | 25 | 20 | 18 | 12 | 8 | 8 | 10 | 29 | 8 | 21 | 20 |
Elongation At Break, % | ≥1100 | 1250 | 1500 | 1400 | 1380 | 1300 | 1050 | 1000 | 1150 | 1150 | 820 |
Shore Hardness, ASTM D2240, Shore A | 40 | 35 | 32 | 25 | 20 | 25 | 35 | 62 | 36 | 36 | 75 |
The versatility of SIS polymers finds expression across a wide spectrum of industries and applications. They are particularly well-suited for formulating pressure-sensitive adhesives, including packaging tape, labels, and medical adhesives. Furthermore, SIS polymers play a pivotal role in hot-melt adhesive formulations, offering excellent bonding properties and thermal resistance.
In the realm of plastics and asphalt modification, SIS polymers contribute to enhancing material properties such as flexibility, durability, and weather resistance. Their compatibility with various substrates makes them valuable additives in the production of hygiene products, packaging materials, and elastic films.
A notable application of SIS polymers is in the development of hot melt Polyisobutene-SIS copolymer pressure-sensitive adhesives for skin contact applications. Leveraging the inherent properties of polyisobutylenes and styrene-isoprene rubbers, these adhesives offer exceptional adhesion to skin and substrates, along with good water resistance. Despite their staining potential and relatively poor recovery from extension, these adhesives provide a reliable solution for medical tapes, transdermal systems, and other skin-contact applications.
In conclusion, SIS (Styrene-Isoprene-Styrene) block copolymers represent a versatile and environmentally friendly solution for a wide range of applications. With their unique combination of properties, including high strength, low hardness, and superior adhesion, SIS polymers continue to drive innovation across industries such as adhesive manufacturing, plastics modification, and hygiene product development. As sustainability and performance become increasingly important considerations, SIS polymers stand poised to meet the evolving needs of modern manufacturing and consumer demands.
Our masterbatches find a multitude of applications across diverse industries. Whether in plastics, textiles, or various manufacturing processes, our masterbatches play a pivotal role in enhancing product quality and performance. With customizable formulations, they offer color consistency, UV protection, flame resistance, and more, making them the go-to solution for countless applications. From automotive parts to packaging materials, our masterbatches are the trusted choice for achieving superior results across a wide spectrum of industries.
Our custom masterbatches are designed to match specific polymers, ensuring optimal performance when incorporated into your selected material. We have the capability to produce masterbatches suitable for a variety of polymers mentioned below, and many more. If you’re working with a material that isn’t listed here, please don’t hesitate to reach out to our knowledgeable technical team to explore the possibility of meeting your specific needs.
Low Density Polyethylene – Somewhat more translucent than HDPE and considerably more pliable, primarily employed in flexible packaging, tote bags, pliable tubing, film applications, and similar uses. Like HDPE, it has limited transparency characteristics. It exhibits outstanding chemical resistance to alcohols, acids, and alkalis but has restricted resistance to hydrocarbon solvents and mineral oils. Prolonged exposure to UV radiation can initiate degradation.
High-Density Polyethylene – Featuring a somewhat milky-white appearance, this material finds wide application in rigid bottle packaging, injection-molded caps and closures, crates, and more. Its natural opacity can limit the degree of transparency attainable. HDPE exhibits superior chemical and solvent resistance when compared to LDPE.
PPCO Random & PPHO – A polymer with moderate clarity, employed in the production of caps and closures. It is also utilized for crafting household items, buckets, toys, and storage containers. Polypropylene offers flexibility without significant limitations on color or special effects. Random copolymer boasts greater clarity compared to homopolymer and is better suited for creating translucent shades.
PPCO Block – Similar to PPCO but enhanced for increased impact resistance. An additive renders the polymer white, resulting in high opacity. This characteristic may limit the achievable transparency.
Polyethylene Terephthalate (PET) – Polyester materials exhibit robust mechanical strength along with excellent chemical resistance and barrier properties. PET is frequently chosen for the production of carbonated beverage containers. Moreover, polyester can be spun and employed in textile manufacturing for clothing. PET is highly transparent, making it an excellent choice for translucent packaging, although a subtle hint of “yellowing” may impact extremely light tints.
Polybutylene Terephthalate – A crystalline thermoplastic engineering polymer frequently employed as an insulating material within the electronics sector. This substance belongs to the polyester category, showcasing a remarkable equilibrium of attributes and processing qualities.
General Purpose Polystyrene – Exhibiting a glass-clear appearance but possessing minimal impact resistance, this material finds its primary application in CD cases. Its notable clarity renders it suitable for creating translucent hues, although an occasional violet tint may be discernible.
High Impact Polystyrene – Derived from GPPS by incorporating an impact-enhancing agent to boost its resistance to impacts. This added component results in the polymer becoming white, and different formulations provide varying degrees of opacity. Typically employed in the fabrication of game pieces, toys, and similar items. Its pronounced whiteness can pose challenges when aiming for translucent coloration. Specialized alternatives like K-Resin and Styrolux are accessible in the market to attain the same level of translucency as GPPS.
Acrylonitrile Butadiene Styrene (ABS) – A more robust iteration of High Impact Polystyrene (HIPS) employed in high-value components. ABS exhibits greater durability compared to HIPS-made components, although it encounters similar challenges when attempting to achieve translucent colorations. Just like HIPS, ABS offers specialized translucent variants. Owing to its durability, ABS is commonly used in crafting casings for power tools.
Polyamide (6, 66) – Nylon represents a versatile grade extensively employed in mechanical construction and maintenance. Its popularity stems from its excellent blend of mechanical strength, rigidity, mechanical damping characteristics, and effective electrical insulation capabilities. Consequently, nylon is a preferred material for manufacturing electrical enclosures. PA66 serves as a common alternative to metal across diverse applications, with its chemical and physical attributes closely resembling those of PA6. PA6 exhibits superior impact resistance and resistance to solvents, albeit with a heightened susceptibility to moisture absorption.
Styrene Acrylonitrile Copolymer – Possessing transparency and outstanding chemical and heat resistance, SAN also boasts good rigidity, tensile strength, and flexural strength. Thanks to its high-gloss finish, SAN is commonly chosen for cosmetic packaging purposes. However, achieving light tint colors with SAN can be challenging due to the violet dyestuffs inherent in the material, which are utilized to enhance its visual appearance during manufacturing.
Polyethylene Terephthalate Glycol – PET with the incorporation of glycol. This glycol addition enhances flow properties but diminishes strength. PETG can be extruded to create bottles and can be formed into sheets for producing ‘blister’ style packaging.
Thermoplastic Elastomer (TPE) or Thermoplastic Polyurethane (TPU) – TPU finds diverse uses in applications such as automotive instrument panels, caster wheels, power tools, medical devices, as well as various extruded film, sheet, and profile applications. TPEs are employed across a wide range of applications in industries spanning automotive, medical, construction, electrical, appliances, packaging, and industrial sectors.
Frequently asked questions about our masterbatch
Masterbatch is used to add colour or enhanced properties to plastic components. It’s a concentrated formula of colourants and/or effects and/or additives, combined with fillers, encapsulated within a carrier plastic resin. Masterbatch is supplied in pellet form to be dosed into raw polymer for use in plastic manufacturing. Masterbatch can be used with virgin polymer or used with recycled plastic. We encourage customers to consider using PCR (post-consumer recycled) resins wherever possible. Want to know more? Check out our detailed article for a deeper explanation of masterbatch and its incredible role in enhancing product colours. Click here to contact us!
Anyone creating a coloured plastic item will tend to require a coloured masterbatch. Our factory can develop and supply plastic colourants in the form of masterbatches, for plastic moulders to use in production. Masterbatch is almost always the preferred choice for colouring plastics. Most coloured plastic components we encounter in our daily lives will be coloured with masterbatch. As the pigments or dyes are encapsulated within a pellet, masterbatch ensures a much cleaner process than would otherwise be experienced by using liquid colours in plastic manufacturing. This can minimise waste and significantly reduce downtime in production. It also allows very accurate control of colour dosing and distribution. It’s not just about colour though, masterbatches can also be used to achieve a number of special finishes within plastics. Additive masterbatches can improve processing and enhance the properties of end components.
Generally speaking, our factory provides polymer specific masterbatches for use in HDPE, LDPE, PPCO, PPHO, PET, PBT, GPPS, HIPS, ABS, PA66/PA6, SAN, PETG and TPE/TPU. Our universal colour range is designed for use in a variety of polymers. We can customize the masterbatch as same as our clients require.
Anyone creating a coloured plastic item will tend to require a coloured masterbatch. Our factory can develop and supply plastic colourants in the form of masterbatches, for plastic moulders to use in production. Masterbatch is almost always the preferred choice for colouring plastics. Most coloured plastic components we encounter in our daily lives will be coloured with masterbatch. As the pigments or dyes are encapsulated within a pellet, masterbatch ensures a much cleaner process than would otherwise be experienced by using liquid colours in plastic manufacturing. This can minimise waste and significantly reduce downtime in production. It also allows very accurate control of colour dosing and distribution. It’s not just about colour though, masterbatches can also be used to achieve a number of special finishes within plastics. Additive masterbatches can improve processing and enhance the properties of end components.
A colour match will usually be free, we’ll do the match and post sample plaques free of charge. On rare occasions where specialist constituents are needed to complete the match then our factory will be in touch to discuss any associated costs before we start work.
It will usually take our team 3-5 working days to dispatch a color match sample following receipt of a new color match request. Our team process several matches every day, if we have an exceptionally high volume of matches to produce then leadtimes may be longer. We advise all customers to request matches as soon as they can, in order to avoid any delays.
In many cases, small samples can be obtained free of charge. Please call us to discuss your requirements. Postage costs for samples will be dependant on location.
A color sample from our universal range can often be delivered on a next day service. If you request a sample for a custom color match then this will typically be dispatched within 5-7 working days of receipt of that request, along with your sample plaques.
Universal masterbatch: 1kg
Custom masterbatch: 5kg
Custom compounds: 25kg
Universal roto powders: small lots available in multiples of 20kg
Custom roto powders: 1,200kg
Universal masterbatch: from one working day (dependent on current stock availability)
Custom masterbatch: from five working days (dependent on current production schedules)
Custom compounds: from five working days (dependent on current production schedules)
Universal roto powders: from one working day (dependent on current stock availability)
Custom roto powders: from three weeks (dependent on current production schedules)
Please remember to allow time for delivery. Our deliveries are reliant on external courier services.
©2023. Masterbatch Manufacturer All Rights Reserved.
Our team will send back the best offer in 20 minutes.