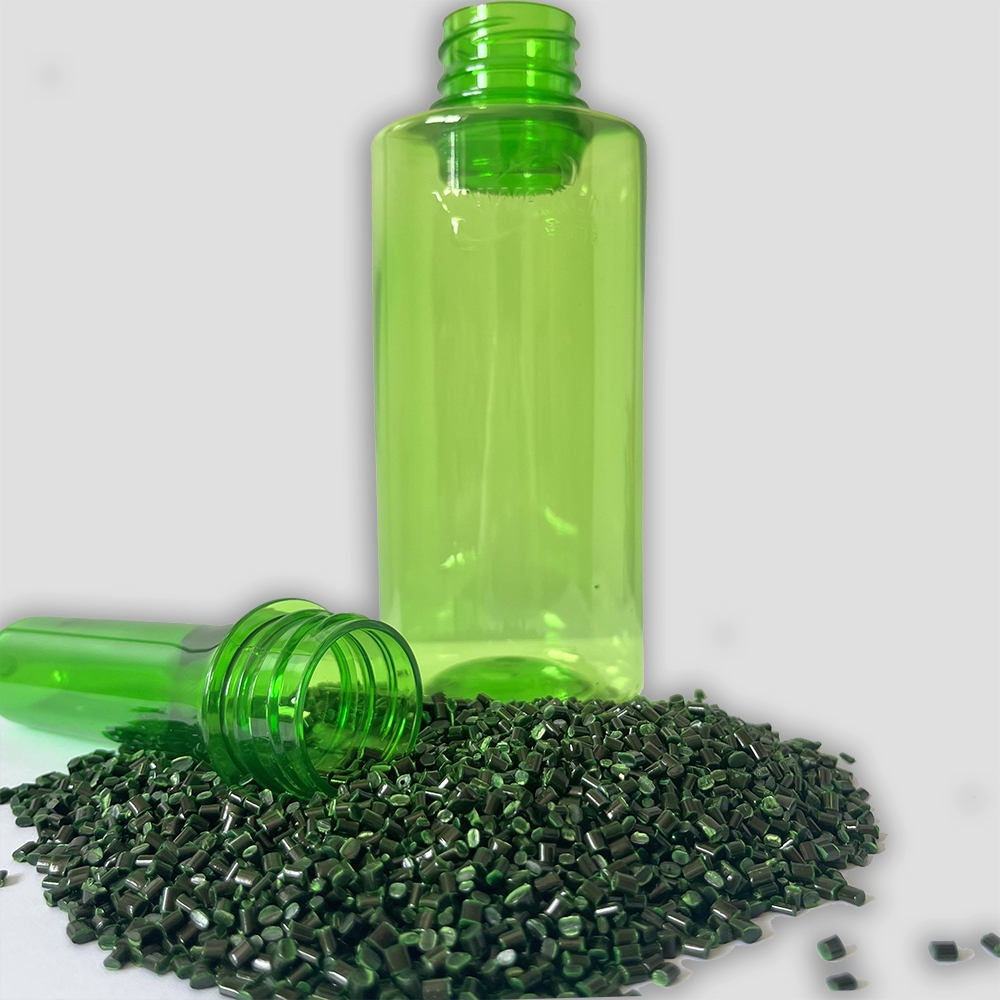
Revelando la excelencia: Masterbatches de PET de alta calidad de Xinwancai
Xinwancai Masterbatches está a la vanguardia a nivel mundial en PET Masterbatches, una línea de productos muy solicitada. Estos masterbatches cuentan con un amplio espectro de colores vibrantes y lujosos, a menudo inalcanzables mediante técnicas convencionales de pigmentos o tintes.