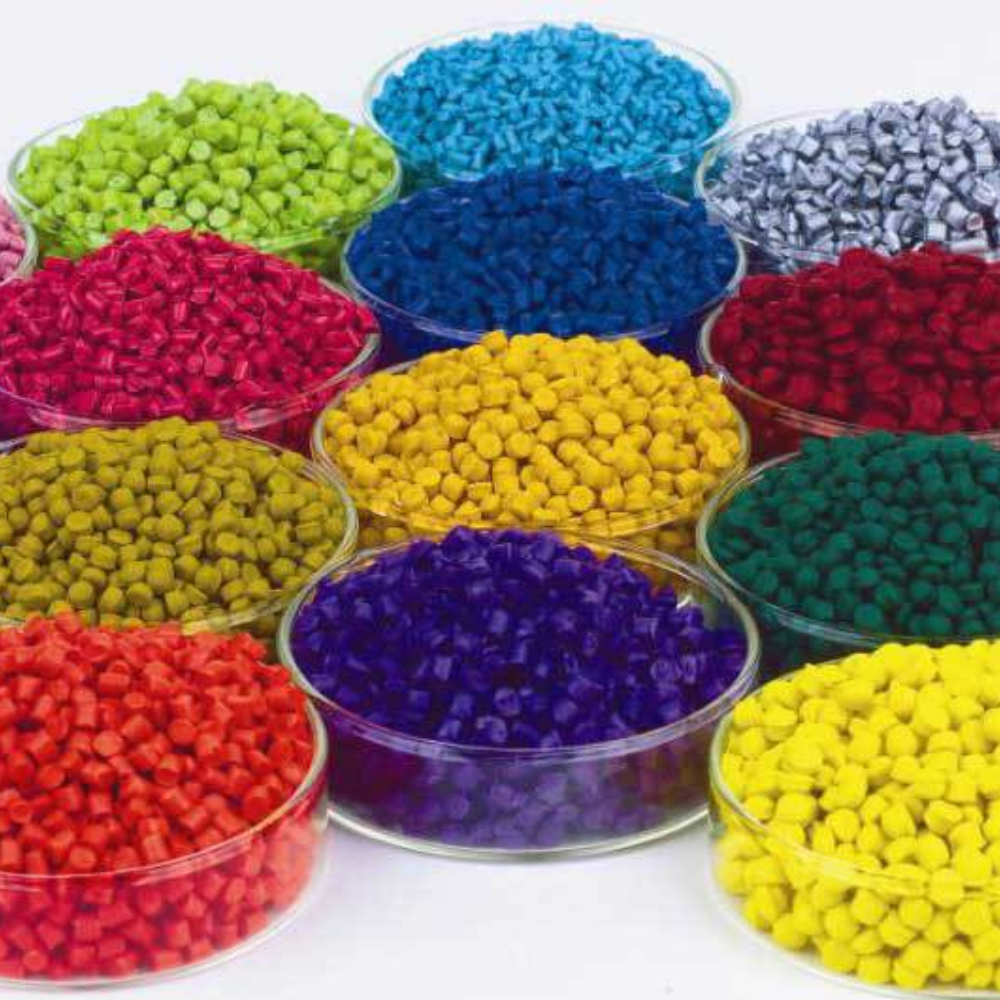
Color Masterbatch – Understanding its Primary Components and Uses
Color masterbatches, also known as color concentrates for plastics, are plastic granules primarily employed for plastic coloring.
Achieving effective dispersion of additives or pigments requires a carrier that effortlessly melds with the base polymer. Moreover, the carrier should accommodate the desired additive or pigment load. From a cost-efficiency standpoint, a more concentrated carrier minimizes the quantity of masterbatch needed for blending with the base polymer.
To preserve the essential characteristics of your masterbatch, the carrier must exert minimal influence on the base polymer matrix. Consider the transparency of polyester resins like PET and polycarbonate (PC). Any additive integrated into the base polymer must exhibit exceptional transparency on its own and remain fully compatible with the base polymer to avert haziness or loss of clarity.
In the case of PC resins, maintaining heat resistance is paramount, especially in applications like automotive components, where high transparency and heat resistance are fundamental.
Identifying polymers that can serve as an effective carrier without compromising the properties of the base polymer can be a challenging quest. To surmount this challenge, our factory has introduced our own optimal carrier, a groundbreaking co-polyester characterized by its sparkling transparency and exceptional heat resistance.
Our factory offers three distinct grades of optimal carrier to cater to diverse requirements: optimal carrier 90, 100, and 110. Among these, optimal carrier 90 exhibits full compatibility with PET and PETG, making it an ideal choice for polyester masterbatches. Optimal carrier 100 and 110 demonstrate miscibility with PC at all concentrations, resulting in transparent blends, rendering them suitable for polycarbonate masterbatches.
High heat resistance and transparency are not the sole benefits of employing optimal carrier as a masterbatch carrier. Optimal carrier boasts high melt strength and a wide processing window, enabling the addition of fillers while preserving melt properties. This facilitates rapid and efficient production processes.
Our optimal carrier can be processed at lower temperatures compared to crystalline polyesters and PC. This not only aids in averting thermal degradation of sensitive additives but also reduces energy consumption during masterbatch processing.
Optimal carrier, being fully amorphous, not only maintains transparency when used with PET but actually enhances it. The issues of whitening, often observed at the injection points of PET articles due to PET’s semi-crystalline nature, can be mitigated or entirely eliminated by incorporating as little as 10 to 20% of optimal carrier 90.
Stress cracking is a known issue in polycarbonate articles, especially after repeated tensile loading stress. It can compromise the visual and mechanical properties of PC parts and, in extreme cases, lead to fractures with serious consequences, particularly in automotive applications. The introduction of polyesters to PC is a recognized method to reduce the risk of stress cracking. Optimal carrier 100 and 110 can be used in PC to improve processability without compromising transparency and with only a minor impact on heat resistance.
Optimal carrier is fully approved for food contact applications in Japan (JHOSPA), the United States (FDA), and the European Union (EC 10/2011). Therefore, it is a suitable choice for masterbatches used in food packaging and other applications involving food contact.
Learn more knowledge and trends in masterbatch industry from our blog.
Color masterbatches, also known as color concentrates for plastics, are plastic granules primarily employed for plastic coloring.
Revolutionizing the realm of PET packaging, Frost Effect masterbatches elevate clear resins and PET materials during stretch blow molding and thermoforming.
Odor Neutralizer Masterbatches represent a cutting-edge solution designed to absorb and minimize unwanted odors emitted by recycled polymers and products exposed to constant humidity and moisture.
©2023. Masterbatch Manufacturer All Rights Reserved.
Our team will send back the best offer in 20 minutes.